Loss of gyro input causes loss of position
Case narrative:
A DP 2 vessel was involved in ROV operations in deep water with good visibility. The environmental conditions were moderate with a wind speed of 15 Knots and a current speed of 1.2 knots during the time of event. The vessel was operating in open bus tie mode with two redundant groups. There were five (05) thrusters and four (04) generators installed on the vessel and all were selected to DP. There were three (03) gyros, two (02) position reference systems and two wind sensors available and all selected to DP.
The following diagram depicts the system configuration prior to the event:
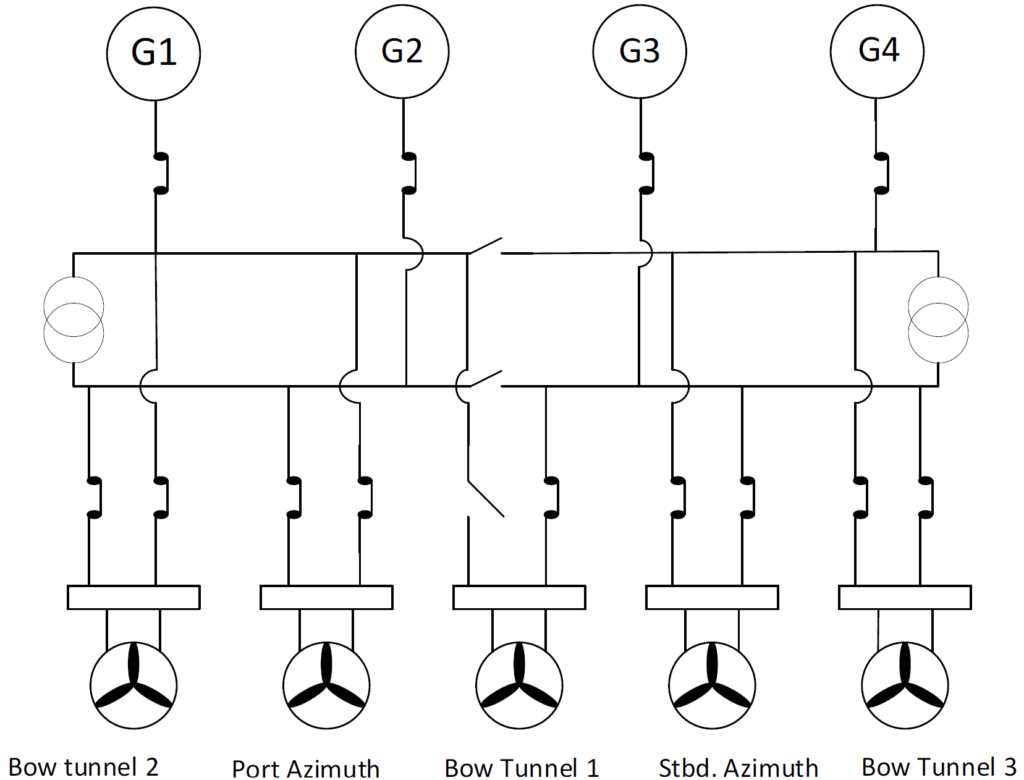
The event: An alarm “Gyro 2 Not Ready” appeared and gyro 2 was automatically deselected from the DP system. Immediately after this, gyro 1 also dropped out with alarms, “Gyro 1 Not Ready” and “Gyro 1 Heading Dropout”. Within one second the third gyro failed with the following alarms in succession, “Gyro not enabled”, “All Reference systems rejected” and “Position Dropout”.
It was noted that gyro 1 repeater on the bridge continued to display the correct heading, while heading input from gyro 1 was missing at the DP operator station (OS). Concurrently, it was further noticed that gyro 2 repeater was in alarm with no heading display and gyro 3 was displaying the heading with 10 degrees offset. Orders were given to recover the ROVs on deck and the vessel control was transferred to full Manual mode.
The crew managed to get the vessel back to full DP control within twenty-eight (28) minutes from the onset of the first failure with one hundred and fifty (150) metres of uncontrolled movement during that time.
The following actions were executed:
- Gyro 2 restarted, rebooted and realignment completed
- DP OS 1 & OS 2 soft rebooted
- Controllers A & B of OS 1 rebooted after which all PRS and DP sensors online and enabled
The investigation revealed that gyro 2 was lost due to the loss of its Interface and Power Supply Unit. After replacing this unit, a test was carried out to prove the independence of gyro 1 from gyro 2. On disconnecting the power supply to gyro 2, it was observed that gyro 1 was also lost. Further system analysis concluded that the gyro 1 ready signal was linked with that of gyro 2 in the DP controller cabinet. This cross-connection issue caused a detrimental effect on both gyros’ performance. In addition, following a malfunction on any gyro, the No. 1 Control and Display Unit would force the gyro 1 ready signal to disappear at the DP operator station. These issues were corrected and tested to the satisfaction of all involved parties.
During the time of the incident gyro 3 sensor value was found to be approximately ten (10) degrees different from gyro 1 and gyro 2 headings. When both gyros 1 and 2 were deselected from DP, gyro 3 was selected to the DP system. However due to the large deviation in the heading value of gyro 3 compared with the estimated heading, which in this case should not have been more than two degrees, the DP controller rejected gyro 3.
The lessons
- If a gyro has a static deviation from other gyros, this should have been identified, investigated, and rectified so that all gyros’ measured headings are within the DP control system limits to avoid any such problems
- The common mode failure related to the ready signal of gyros’ 1 and 2, should have been identified during commissioning, FMEA proving trials and DP annual trials programme. IMCA documents M 166, “Guidance on Failure Modes & Effects Analyses (FMEAs) and M 190, “Guidance for Developing and Conducting DP Annual Trials Programmes”, underline the importance of having robust FMEA and set of annual trials
- IMCA M 252 “Guidance on Position Reference Systems and Sensors for DP Operations” provides general information on use of reference systems and the good practice of multiple references and sensors
- Importance of proper investigations and robust testing of cross connections in redundancy groups of DP vessels is highlighted in this case study
This case study demonstrates the importance of robust testing procedures during FMEA proving trials, annual trials or 5-yearly trials program. The case study also highlights the importance of conducting daily compass checks and completion of all other operational checklists so that differences in redundancy groups are identified early and can be corrected.
DP Event
Published: 28 September 2020
Download: IMCA DPE 03/20
Submit a Report
The following case studies and observations have been compiled from information received by IMCA. All vessel, client, and operational data has been removed from the narrative to ensure anonymity.
Case studies are not intended as guidance on the safe conduct of operations, but rather to assist vessel managers, DP operators and DP technical crew in appropriately determining how to safely conduct their own operations. Any queries should be directed to IMCA at [email protected]. Members and non-members alike are welcome to contact IMCA if they have experienced DP events which can be shared anonymously with the DP industry.
IMCA’s store terms and conditions (https://www.imca-int.com/legal-notices/terms/) apply to all downloads from IMCA’s website, including this document.
IMCA makes every effort to ensure the accuracy and reliability of the data contained in the documents it publishes, but IMCA shall not be liable for any guidance and/or recommendation and/or statement herein contained. The information contained in this document does not fulfil or replace any individual’s or Member's legal, regulatory or other duties or obligations in respect of their operations. Individuals and Members remain solely responsible for the safe, lawful and proper conduct of their operations.