Lack of Experience in Dealing with Environmental Conditions Caused Loss of Position
Case narrative:
A DP 2 vessel with two redundant groups and operating in open bus mode, was involved in drilling operations in water depths of approximately 38 metres. The vessel was performing cone penetration testing (CPT) at a location with a drilling depth up to 90 metres. There were six thrusters and four generators available onboard and all were selected to DP. The available position reference systems (PRS) onboard were three DGNSS, one taut wire and one HPR, out of which only two DGNSS were selected to DP.
Also, out of the available four wind sensors, three of them were selected into DP, along with three gyros and three motion reference systems. The visibility was reported to be good with wind speed of fifteen knots at 045˚, current speed of four knots at 040˚and swells of 2 metres height with a duration of ten seconds at 220˚ were recorded during the operation. At the time of the incident, the vessel was drilling at a depth of 54 metres.
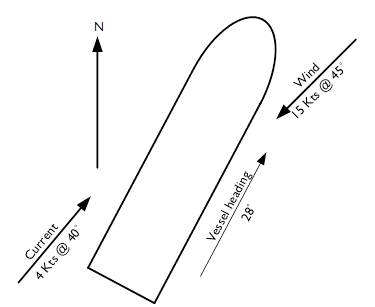
The vessel was encountering strong currents from the stern, as expected, and experienced by the DPO’s during the earlier spring tides. For this reason, the vessel receives location specific current modelling from a remote centre during its operations. These models display peak marine current’s direction and speed at any given time. During these strong currents, it is prudent to change the vessel heading regularly to follow the currents direction and to keep them at the stern.
The Event
At 20:00 hrs the senior DPO took over the watch at the DP desk and at 20:10 noticed the current was changing direction and intensity. The vessel heading was changed from 020˚ to 024˚ to keep the current at the stern. After the heading change, the loading on the vessel’s thrusters were observed to be within normal operating limits and the vessel maintained its position. At 20:45, the SDPO noticed another change in the direction and speed of the current, and further observed that the load was increasing on all thrusters. The drilling control was advised of the need to make a further heading change as the CPT operation was ongoing.
At 20:54 the DP consequence analysis advised that the load was higher than one of the two redundancy groups could tolerate post worst-case failure. Ten seconds later, power consumption was within limits again. The SDPO advised the drilling control of a further heading change which was confirmed at 20:56, and the heading was changed from 024˚ to 028˚. At 21:00 the DP consequence analysis warning indicated that the power online was in excess of the capacity of one redundant group, post worst-case failure. This alarm lasted for one and a half minutes. After completion of the heading change and at 21:05, the loading on the vessel’s thrusters were observed to be within normal operating limits and the vessel maintained its position. The SDPO handed over the watch to the DPO.
At 21:15 the DPO alerted the SDPO that the load on thrusters T3 and T4 were increasing. The SDPO, immediately attended the DP desk, noticing that thrusters T3 and T4 loads were increasing and that the vessel was struggling to maintain its position. At 21:19 the heading was changed by 2˚ to 030˚. At 21:21 the DP system indicated high loads on T3 and T4 followed by a consequence analysis “Off -Position” warning alarm. Simultaneously, there were speed feedback faults on both T3 and T4. At 21:22 a DP yellow alert was given to the drill operators as the vessel excursions overshot the ten percent of the water depth limitation.
The drillers immediately stopped their drilling operation, lifted the drilling equipment, and hoisted it back at the moonpool. The heading was changed to 040˚ where the current was at the vessel’s stern. At 21:25 the vessel settled down and could maintain position. At this time, the drilling assembly was inspected, and the pipe and the bottom hole assembly were observed to be in good condition. After a complete inspection, it was confirmed that there was no damage to the drilling equipment. Distance of uncontrolled movement during the event was nine metres and the duration of the event was recorded to be six minutes.
The lessons
- It needs to be fully understood that the current indicated was the “DP current” and not a “measured current”. A DP current value could be affected by other disturbing factors and needs to be relied on with care with regard to magnitude as well as direction.
- It was mentioned in the report that the current strength was above the thresholds specified in the vessel ASOG. It is essential the ASOG is continually reviewed to ensure it covers all possible hazards during a specific operation.
- IMCA M 220 Guidance on Operational Activity Planning, discusses the importance of various documentations such as CAM, TAM and ASOG. DP and emergency response drills discussed in the document, highlight the importance that all DP personnel must know what actions to take and what to expect when operating parameters are exceeded.
- It is concluded in the report that current must be included as a factor in the vessel’s manual of permitted operations. The effect of the stern thrusters, running at near full power and throwing the wash against the hull, will be reduced due to thruster-hull interaction. The vessel DP capability plots should be consulted.
- It needs to be highlighted that only two position reference systems of the same kind were being used. Therefore, with regard to position reference systems, the vessel was not set up according to DP class 2 requirements. A minimum of three position reference systems with one being of different type are required in a DP class 2 or 3 operation.
- The contents of the ASOG for this operation was not disclosed. However, it was stated in the report that immediately after the yellow alert, drilling operations stopped, and the drilling equipment lifted and hoisted up in the moonpool. It is not clear whether these actions were precautionary measures or mandates arising from the ASOG. In this instance a Yellow alert was indicated to the drill operators, if a loss of position was occurring a Red light should have been given to the drill operators.
- It is not clear in the report as to why the speed feedbacks on both T3 and T4 became faulty. One possibility was that the speed feedback discrepancies of T3 and T4 could have been caused by the strong current inflow and thrusters running at near or above full speed.
This case study demonstrates the importance of fully understanding the vessels capability and normal operating limits, and also ensuring that this level of detail is clear within the ASOG. The case study also highlights the significance of training in emergency situations for key DP personnel.
DP Event
Published: 3 December 2020
Download: IMCA DPE 04/20
Submit a Report
The following case studies and observations have been compiled from information received by IMCA. All vessel, client, and operational data has been removed from the narrative to ensure anonymity.
Case studies are not intended as guidance on the safe conduct of operations, but rather to assist vessel managers, DP operators and DP technical crew in appropriately determining how to safely conduct their own operations. Any queries should be directed to IMCA at [email protected]. Members and non-members alike are welcome to contact IMCA if they have experienced DP events which can be shared anonymously with the DP industry.
IMCA’s store terms and conditions (https://www.imca-int.com/legal-notices/terms/) apply to all downloads from IMCA’s website, including this document.
IMCA makes every effort to ensure the accuracy and reliability of the data contained in the documents it publishes, but IMCA shall not be liable for any guidance and/or recommendation and/or statement herein contained. The information contained in this document does not fulfil or replace any individual’s or Member's legal, regulatory or other duties or obligations in respect of their operations. Individuals and Members remain solely responsible for the safe, lawful and proper conduct of their operations.