Dropped object during crane operations
What happened
A piece of timber fell from a crane jib and landed on deck. The main crane on the vessel was being prepared for lifting operations by four deck crew and the crane operator. When the crane hooks were disconnected, the deck crew moved clear to allow the crane operator to start luffing the jib from the cradle. As the jib was slewing around, the crane operator observed an object fall from a height of approximately 10 metres to the main deck. No-one was nearby – the nearest crew were 15m away from where it landed. The dropped object was identified as a piece of timber, weighing 7.6kg. This had been used in a temporary repair of the dunnage on the boom rest.
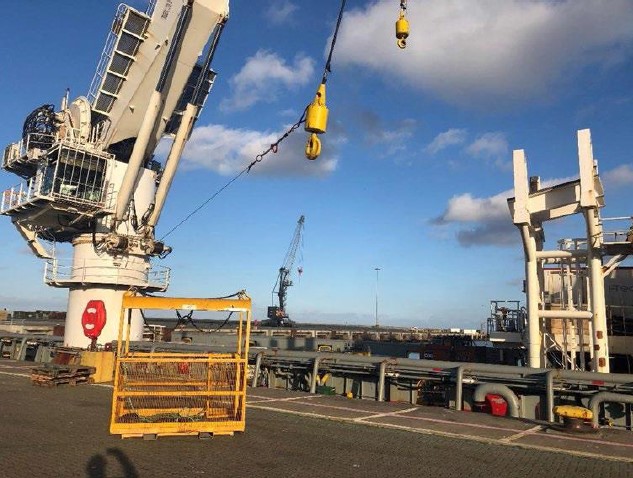
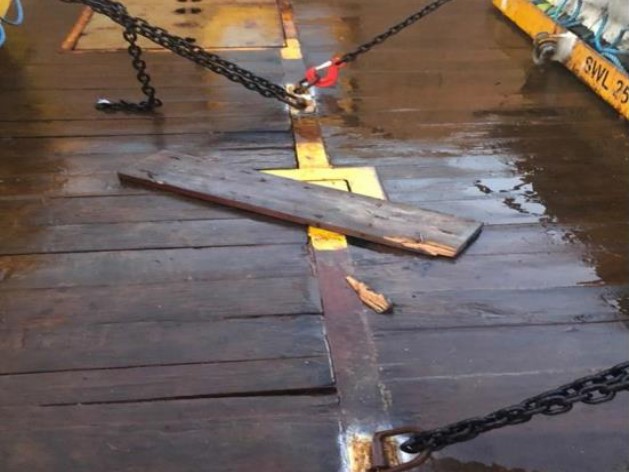
What went wrong?
- Initial design did not sufficiently address the lateral movements of the jib in the boom rest;
- Responsibility for the crane and associated equipment was not clearly understood;
- The temporary repair:
- Several onboard inspections and third-party inspections were conducted which did not identify issues with the support dunnage and subsequent temporary repairs;
- The damaged wooden packer was formally reported nearly a year earlier. This report had been closed out prematurely when a temporary repair was made;
- The temporary repair was put in place using screws rather than bolts to attach a board over the damaged wooden packer. The screws corroded, causing the board to become loose and fall to the deck;
- A work order had not been created for remedial works on the damaged support timbers;
- There was no checklist developed to include inspection of the boom rest.
Actions
- Ensure roles and responsibilities are clearly defined, communicated and understood;
- Review all lifting appliances, supports and cradles. Ensure that the equipment is maintained in its as built condition;
- Confirm that the boom rest is part of the vessel planned maintenance system;
- Ensure crane inspection checklists include inspection of the boom rest;
- Confirm areas around crane boom rests are included in hazard hunts for potential dropped objects.
Members may wish to refer to:
- HSSE 019 Guidelines for lifting operations
- Short videos:
Safety Event
Published: 30 March 2021
Download: IMCA SF 09/21
IMCA Safety Flashes
Submit a Report
IMCA Safety Flashes summarise key safety matters and incidents, allowing lessons to be more easily learnt for the benefit of all. The effectiveness of the IMCA Safety Flash system depends on Members sharing information and so avoiding repeat incidents. Please consider adding [email protected] to your internal distribution list for safety alerts or manually submitting information on incidents you consider may be relevant. All information is anonymised or sanitised, as appropriate.
IMCA’s store terms and conditions (https://www.imca-int.com/legal-notices/terms/) apply to all downloads from IMCA’s website, including this document.
IMCA makes every effort to ensure the accuracy and reliability of the data contained in the documents it publishes, but IMCA shall not be liable for any guidance and/or recommendation and/or statement herein contained. The information contained in this document does not fulfil or replace any individual’s or Member's legal, regulatory or other duties or obligations in respect of their operations. Individuals and Members remain solely responsible for the safe, lawful and proper conduct of their operations.