Failure of EGS valve stem on dive helmet
What happened
A member reported an incident in which the emergency gas system (EGS) valve handle on a commercial diving helmet broke off. At the time of the failure the dive helmet was undergoing pre-dive inspection on deck.
What went wrong
A dive technician stripped the valve and discovered the break to be located at the valve stem – where the threaded portion meets the square section. Both parts of the valve stem, adjacent to the break, were noted to be pitted and a fine hairline crack was noted. The failed component was replaced with a new spare. Following a gas leak and function test, the dive helmet was placed back into service. The failed component was sent ashore for further investigation.
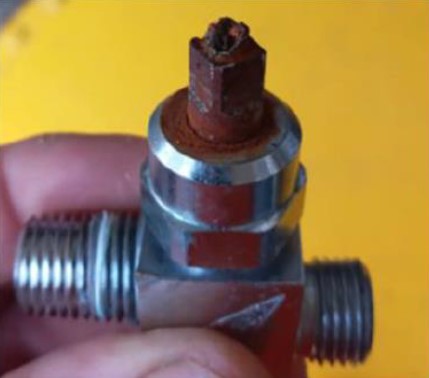
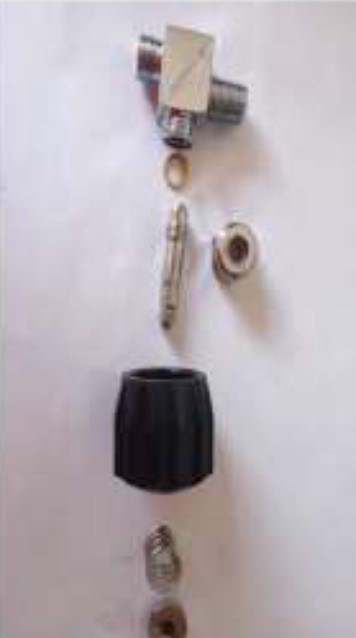

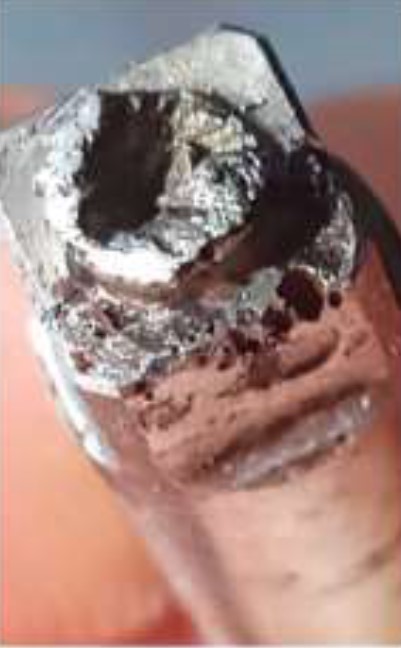
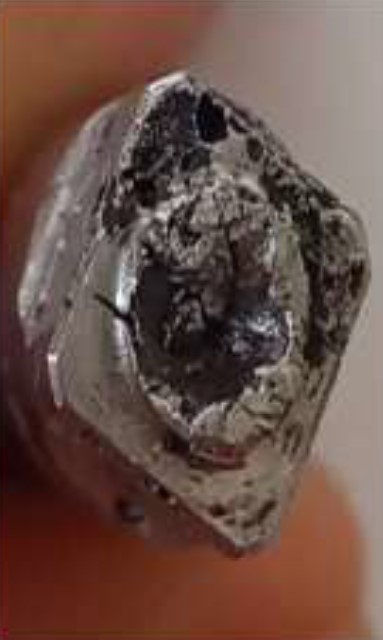
What were the causes?
The member arranged an independent laboratory review of the material to try and identify the root cause. The finalised laboratory report indicated that failure occurred as a result of pitting and stress corrosion cracking under the action of the chlorides present in salt water.
Actions taken and lessons learned
- Following its investigation our member took the following actions:
- The company preventative maintenance system (PMS) was modified to require NDE dye penetrant testing of EGS valve stems for all base and field diving helmets at a minimum of 12 monthly intervals.
- Internal instructions were issued stating that if the post-dive, inspection, or maintenance routines recommended by the manufacturer highlighted any concerns, the relevant valve stem(s) should undergo immediate NDE dye penetrant testing. If any anomalies are then detected, the component should be discarded and replaced.
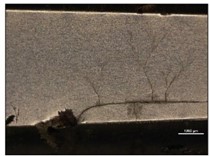
Actions taken and lessons learned
- Following its investigation our member took the following actions:
- The company preventative maintenance system (PMS) was modified to require NDE dye penetrant testing of EGS valve stems for all base and field diving helmets at a minimum of 12 monthly intervals.
- Internal instructions were issued stating that if the post-dive, inspection, or maintenance routines recommended by the manufacturer highlighted any concerns, the relevant valve stem(s) should undergo immediate NDE dye penetrant testing. If any anomalies are then detected, the component should be discarded and replaced.
Since these measures were put in place our member has identified three additional valve stems with stress-like indications in the material. Note the pin hole in this example that our member detected in a rental asset:
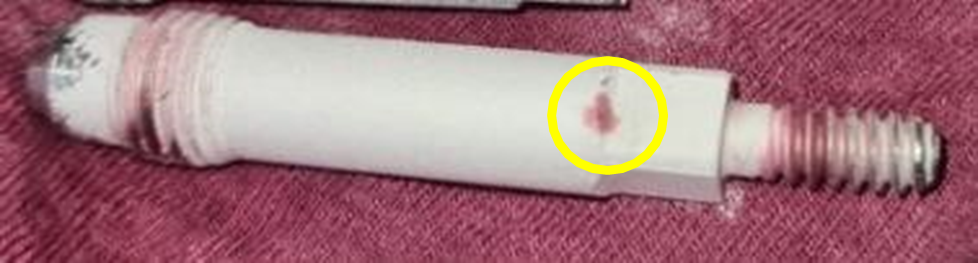
Safety Event
Published: 16 June 2021
Download: IMCA SF 17/21
IMCA Safety Flashes
Submit a Report
IMCA Safety Flashes summarise key safety matters and incidents, allowing lessons to be more easily learnt for the benefit of all. The effectiveness of the IMCA Safety Flash system depends on Members sharing information and so avoiding repeat incidents. Please consider adding [email protected] to your internal distribution list for safety alerts or manually submitting information on incidents you consider may be relevant. All information is anonymised or sanitised, as appropriate.
IMCA’s store terms and conditions (https://www.imca-int.com/legal-notices/terms/) apply to all downloads from IMCA’s website, including this document.
IMCA makes every effort to ensure the accuracy and reliability of the data contained in the documents it publishes, but IMCA shall not be liable for any guidance and/or recommendation and/or statement herein contained. The information contained in this document does not fulfil or replace any individual’s or Member's legal, regulatory or other duties or obligations in respect of their operations. Individuals and Members remain solely responsible for the safe, lawful and proper conduct of their operations.