DP2 Service Operations Vessel (SOV) DP Incident
Case narrative
A DP2 walk to work vessel was operating inside an offshore windfarm manoeuvring into position to permit transfer of people and cargo to a wind turbine by means of a motion compensated gangway system. The DP current at the time of the event was 1.8 knots – 190 degrees and the wind force was 20 knots – 114 degrees. All thrusters were selected online and three of 4 generator were also online, the 4th ready and on standby. There were two separated redundant groups. Two DGNSS, one laser, 3 gyros, 3 VRS and 3 wind sensors were also online.
Note that the vessel was equipped with the following additional references:
- Taut wire – this was not permitted to be used infield due to placing clump weight on the seabed;
- Acoustic position reference – not permitted to be used due to placing equipment on the seabed;
- Microwave reference – transponders not installed prior to approach due to the impracticalities associated with high number of wind turbines.
During the handover of the watch, the SDPO took control and commenced with the DP handover checklist. The vessel was stopped in all movements, outside the 50m radius – abeam from the wind turbine. The laser position reference sensor was operating and set on a target, but not yet enabled in DP. The SDPO initiated a 20m move in order to move slowly inside the 50m radius of the turbine. On finalising of the 6 hourly DP handover checklist, the laser position reference was selected to DP. All reference systems were online and were enabled in DP. The laser position reference was set on “auto tilt” and brightness filter at 60%, blanking zones were set.
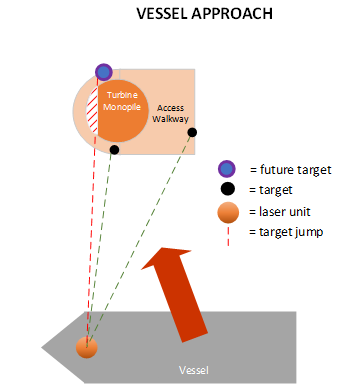
The distance to the tower was 40m when the SDPO commenced a move of the vessel towards the tower in order to get the vessel alongside for walk to work operations. After the move was completed, the SDPO deselected the laser position reference from the DP desk in order to change the laser target. The SDPO changed the selection of the target because it would get obstructed by the railings of the walkway around the turbine when the vessel would move closer. The ‘new’ selected laser target had a clear sight with the laser position reference transponder/receiver unit. Once the laser signal was stable the SDPO enabled it back in DP. Shortly after, the vessel arrived in final position and the SDPO informed the walk to work management team.
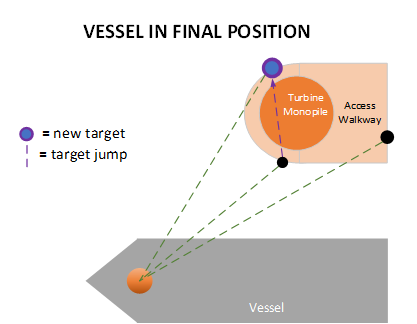
When the SDPO was looking to the reference system main view, he saw that the DGNSS were at the bottom on the edge of the median test line and that the laser reference had disappeared from the view (view range set to 5m). At this time, the DP system alarmed, “Reference prediction error Laser”, and, “Reference median deviation laser”. The SDPO informed the walk to work management team to standby. As the SDPO could clearly see that both DGNSS were operating well, he disabled the laser reference from DP. As expected the vessel started to accelerate towards the tower and the SDPO deselected the sway axis to stop the movement towards the wind turbine.
The DPO controlled the vessel’s speed for sway axis with the joystick and moved 10 meters away from the wind turbine. Sway axis was selected on DP again and an assessment was made in order to use the laser reference again. The blanking zones of the laser reference were slightly adjusted, in order to prevent accidently “jumping” onto false targets. After the laser reference looked stable again, it was enabled on DP and the vessel was moved back in position for walk to work operations. Walk to work operations were completed with no further station keeping issues.
During the station keeping event, the maximum position excursion towards the wind turbine was around 2 meters and heading deviation around 2 degrees.
The Lessons:
- The fast acting response of the crew undoubtedly prevented this event from becoming more significant.
- The planning of the use of position references is of key importance in such an operation where there is a relatively small target area such as a monopile of a wind turbine. The smaller the area, the more challenging the risk of target jumping becomes. The number and placement of targets is of paramount consideration.
- The use of difference sensor technology may have avoided this event. For example, microwave position references.
- The event report did not highlight the use of activity specific operating guidelines nor any change to DP status during the DP event.
This case study demonstrates the importance of careful selection and planning in the use of position reference sensors and the potential consequences therein.
DP Event
Published: 18 June 2021
Download: IMCA DPE 02/21
Submit a Report
The following case studies and observations have been compiled from information received by IMCA. All vessel, client, and operational data has been removed from the narrative to ensure anonymity.
Case studies are not intended as guidance on the safe conduct of operations, but rather to assist vessel managers, DP operators and DP technical crew in appropriately determining how to safely conduct their own operations. Any queries should be directed to IMCA at [email protected]. Members and non-members alike are welcome to contact IMCA if they have experienced DP events which can be shared anonymously with the DP industry.
IMCA’s store terms and conditions (https://www.imca-int.com/legal-notices/terms/) apply to all downloads from IMCA’s website, including this document.
IMCA makes every effort to ensure the accuracy and reliability of the data contained in the documents it publishes, but IMCA shall not be liable for any guidance and/or recommendation and/or statement herein contained. The information contained in this document does not fulfil or replace any individual’s or Member's legal, regulatory or other duties or obligations in respect of their operations. Individuals and Members remain solely responsible for the safe, lawful and proper conduct of their operations.