Dropped object – unexpected release of spool
What happened?
During offshore installation activities there was an unexpected release of the load resulting in it falling to the seabed. The incident occurred during the relocation of a spool from the riser base to the Pipeline End Manifold (PLEM). The operation was conducted from a members’ installation vessel crane, with a third-party provided 52Te lifting yoke previously used in the installation of the spool in 2011 and recertified for use.
What went wrong
Our members’ findings indicated the following:
- “Stop knobs” were not retracted resulting in significant unplanned forces being applied to the yoke structure causing yoke integrity failure and subsequent failure to secure the load (spool);
- Third-party written procedures for installation and commissioning of the third-party subsea equipment were not followed and were not completed;
- Company personnel had limited expertise with the use of the tooling used and relied on heavily on the third-party contractor to confirm that all steps in the commissioning procedure were completed;
- There was a misunderstanding in verbal communications in that company personnel thought that the “stop knobs” had been retracted, but they had not been retracted;
- By design the main Yoke pins were the weak points in the lifting configuration.
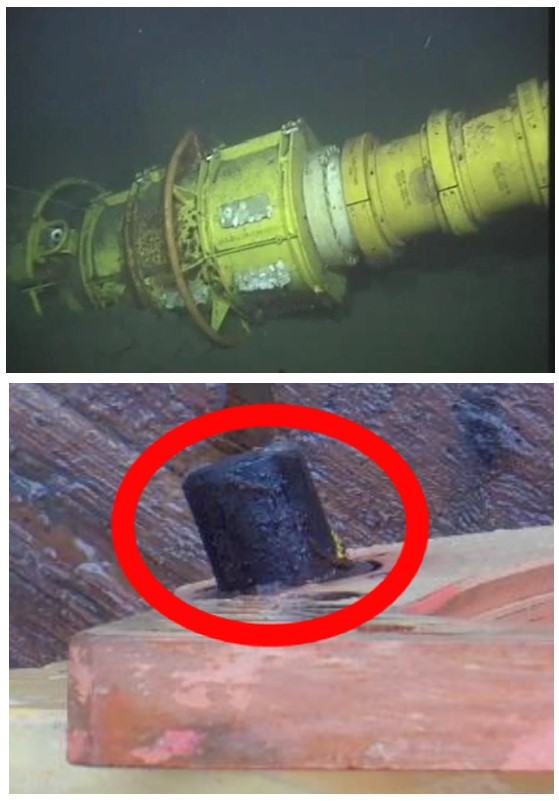
Actions
- Ensure that tooling design arranges for clear visual indicators on the tooling; and that the fail-safe design of their tooling has been considered;
- Reiterate to third-party contractors the importance of following tasks as per procedure;
- Check and carefully verify the competency, experience, and training of third-party contractor personnel;
- Check to ensure that there is no overlap or duplication between third-party contractor procedures and company procedures;
- In task planning, consider further detail, checking and verification for areas that may be unfamiliar;
- Ensure that risk assessments cover the interfaces or gaps between third-party contractor equipment and procedures, and company equipment and procedures.
Members may wish to refer to:
Safety Event
Published: 19 August 2021
Download: IMCA SF 23/21
IMCA Safety Flashes
Submit a Report
IMCA Safety Flashes summarise key safety matters and incidents, allowing lessons to be more easily learnt for the benefit of all. The effectiveness of the IMCA Safety Flash system depends on Members sharing information and so avoiding repeat incidents. Please consider adding [email protected] to your internal distribution list for safety alerts or manually submitting information on incidents you consider may be relevant. All information is anonymised or sanitised, as appropriate.
IMCA’s store terms and conditions (https://www.imca-int.com/legal-notices/terms/) apply to all downloads from IMCA’s website, including this document.
IMCA makes every effort to ensure the accuracy and reliability of the data contained in the documents it publishes, but IMCA shall not be liable for any guidance and/or recommendation and/or statement herein contained. The information contained in this document does not fulfil or replace any individual’s or Member's legal, regulatory or other duties or obligations in respect of their operations. Individuals and Members remain solely responsible for the safe, lawful and proper conduct of their operations.