Predictive Maintenance, the Aviation Industry and Offshore Applications
Maintenance model development
To remain safe and in good working order, all mechanical and electrical systems require some form of regular maintenance to be carried out. Some systems comprise safety critical components, such as heavy lift systems or aircraft engines, and require much more stringent maintenance, assessment and testing to ensure they remain serviceable, and function correctly as intended.
Mechanical and electrical systems may require some form of regular lubrication, inspection for wear or damage, filter maintenance, checks for complete and correct assembly, correct timing and tension of drive belts or chains, correct pressure operation and relief settings, correct voltage, current and power settings, material state of hoses, power and signal cables, correct operation, and structural integrity. Water, dust, or oil ingress can deteriorate these systems and cause corrosion and lead to poor operation or failure and therefore need to be removed.
Depending on the type and use of the equipment, maintenance schedules are usually required on a daily, weekly, monthly basis. Some equipment, such as ROV, require robust checks before and after use. Aircraft, require stringent inspections before and after each flight.
Even out of service items require regular maintenance procedures to ensure they can be quickly brought into operation if needed.
Failure to maintain equipment in good order will lead to reduced performance, increased maintenance costs, premature and expensive catastrophic failure that could result in fatalities. It is therefore imperative that equipment is checked, tested, assessed, and maintained in good working order.
Unplanned (Reactive or Failure based) Maintenance
Traditionally, maintenance systems were concerned with repairing a system after it, or a component part had failed. Known as reactive maintenance, it is inefficient and, since repair occurs after an event, other components could be damaged or severely worn and the repair time and costs may be longer and larger than necessary.
Planned (Scheduled or Age based) Maintenance (PM)
Variously known as preventative or proactive maintenance, in such maintenance systems component failure is assumed to be time based and relies on historical data to determine the maintenance schedule. If the average failure time for a component is 5,000 hours, then the component would be changed, or at least checked, at perhaps 4,000 operating hours to assess its current state. As experience is gained, with the various components, and likely failure times and rates are better understood, components could be replaced on a periodic, time-based system. Preventative maintenance can be costly and inefficient. Worn or damaged components are correctly identified but many are replaced earlier than needed, which increases costs and down time. Some components are not replaced but dismantled for inspection and assessment. Although this system can identify problems before a failure occurs, the constant dismantling of components can cause more damage than the wear cycle to components.
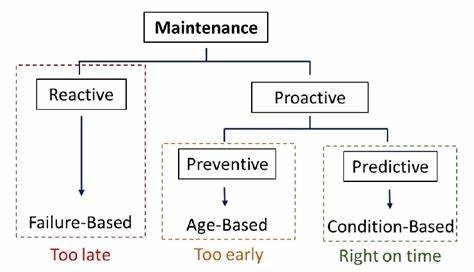
Predictive (Condition based) Maintenance (PdM)
This is a modern maintenance system which requires up to date knowledge of the current state of the system components. The actual state of the equipment determines what maintenance is necessary and when. The system relies on the analysis and use of sensors and data, combined with the various reports from operators and maintainers.
PdM and the aviation industry
Commercial airlines need to maximise the use of their aircraft. A non-operational aircraft is a financial liability to the operating company. An aircraft on ground (AOG) situation, where the aircraft cannot be flown due to an anomaly, or defect, deemed serious enough to ground the aircraft, can be costly. Not only does a replacement aircraft need to be sourced, possibly relocated, compensation to passengers may be due and the unserviceable aircraft repaired, company image may also be damaged. The use of data analysis to accurately predict system condition and prevent unscheduled maintenance has been used for many years in aviation. Originally, the OEM’s of various aircraft equipment drove the use of such data analysis. In the 1990’s Boeing, used its In-Service Data Program in collaboration with its 777 aircraft customers to share operational data to improve the availability and reliability of the aircraft. While these analytical data systems were successful, it is not until relatively recently that more sophisticated “real time” predictive maintenance software tools were introduced. Air France/KLM’s engineering and maintenance released Prognos in 2015. Boeing’s, Boeing Analytx and Airbus’s Skywise were both introduced in 2017. Collins aerospace Ascentia system is reported to show a 30% decrease, in delayed and cancelled flights, due to the real time monitoring of components and systems on the 787 Dreamliner fleet and a 20% decrease in unscheduled component removal on the 777 aircraft fleet. The Prognos system is also able to retrieve data from the aircraft whilst in-flight and during turnarounds (the servicing carried out between flights).
Known more generally as Aircraft Health Monitoring (AHM) the use of predictive maintenance software tools has produced some impressive results, but there are some drawbacks. Research, conducted in 2016, has suggested that by 2026 the global aircraft fleet could generate 98 million terabytes of data annually. Much of this information will be useful but, with such large amounts of data, it is not currently clear how the data, from many different sources, can be synchronised and integrated to become useful.
As an example, an Airbus A350 aircraft has 6000 sensors producing 2.5 Tb of data every day. Everything from fuel flow, pressure and temperature to altitude, speed, weather, and air temperature are monitored. This real time data is combined with historical data and analysed to provide a maintenance schedule to give maximum aircraft availability and reliability.
Rolls Royce IntelligentEngine Engine Health Monitoring (EHM) system can now monitor engine line replaceable units (LRU’s) and prepare and schedule replacements. Essentially the engine can “talk back” in real time to an operational centre and will respond to information requests concerning data for specific parts of the engine system.
Modern AHM systems can not only evaluate the aircraft systems condition, predict, and schedule when maintenance is required but can also link to the supply chain and arrange the appropriate spares at the correct location and ensure that all the necessary conditions are met for the servicing.
The use of these data driven and data mining technology to support maintenance have transformed the aviation industry. Predictive maintenance in aviation has:
- Improved operations by:
- More efficient forecast and management of inventory
- Better management of available resources
- Reduced costs by:
- Minimising the time equipment is being maintained
- Minimising the hours lost to maintenance
- Minimising the cost of spare parts and supplies.
PdM in the Offshore O&G sector
Due to the competitive nature of the aviation industry, it is easy to understand why PdM is a very attractive system, but does it have relevance to the offshore industry?
PdM is very relevant and has been employed, to a limited extent, in the Offshore O&G industry, mainly in the processing of products, for almost 20 years.
Like the aviation industry, O&G companies have been under severe pressure to remain competitive. The industry is just starting to recover from the severe downturn which began in 2014. Significant operator and stakeholder losses have resulted in indefinite delays to planned projects, bankruptcies, and job losses. The survivors were, in the main, those who manged their operational expenses more strictly and efficiently.
Maintenance is a critical, and ongoing, activity in any technical environment and, when done efficiently, assists the productivity and profitability of assets. Much of the O&G infrastructure is ageing, legacy equipment and to retro fit modern sensor systems, to allow for predictive maintenance, could prove expensive and not bring much gain. Systems currently being planned and designed will almost certainly incorporate the sensors systems required to allow for PdM. Prior to the slump, PdM systems were being incorporated into the projects being planned, highlighting the understanding that these systems are of benefit to the industry.
This is supported by McKinsey who estimate that 23% of the potential maximum offshore production capacity is being lost, representing $60B which could, using data analytics in maintenance be recovered. Spark predict, in their “Improving Offshore Production with AI based Analytics” cite a major oil platform operator who have identified bottlenecks in their fluid separation processes which directly impact their production output. They have observed 5 to 10 unique equipment failure events annually, which resulted in a 10–15% downtime and $8M of lost production for each event. Analysis showed that these failures were attributed to 3 components each of which were monitored by independent instruments and no synchronisation of data. A data driven analysis system was implemented with the result that the operator has been able to increase efficiency, highlight other areas of concern, detect anomalies in advance and resolving before they escalate to becoming a major problem and is now expanding the use of PdM to all its platforms.
Essentially PdM, as in the aviation industry, gives an oil company the benefit of being able to:
- More accurately predict maintenance requirements,
- Reduce unnecessary component replacement
- Minimise downtime
- Increase production
- Reduce unnecessary servicing and replacements
- Improve overall efficiency
- Reduce overall production costs
PdM and the Offshore Renewables sector
The renewables sector, being relatively young, has been better positioned to employ data driven systems into its infrastructure design, construction, and maintenance. Although relatively simple in design, a wind turbine installation needs a large array of sensors to monitor the various mechanical and electrical variables. Shaft, gear and bearing balance, friction, wear, damage, lubrication and temperature, wind speed and direction additionally wind turbines can be susceptible to lightning strikes, defective rotor blades and tower movements. It may be necessary to shut down the turbine rapidly to prevent further damage. Real time sensor data and analysis is critical to be able to manage the turbines efficiently and PdM offers the means to achieve this, additionally output loads can also be matched to demand more efficiently. The wind industry adopted PdM early and all installations are designed to incorporate data monitoring sensors.
PdM in support of offshore installations
The arguments supporting the use of PdM, in both the O&G and Renewables sectors, can be extended to their use in equipment supporting offshore operations. Downtime, caused by breakdowns in vessels and ROV’s for instance, can severely impact project deadlines, production targets and increase project costs significantly. PdM, when applied to vessel maintenance can provide much more efficient support with reduced downtimes and improved costs and efficiency.
Conclusion
The use of a comprehensive data driven analysis systems to predict and manage maintenance have demonstrated considerable benefit wherever they have been incorporated. It is most efficient when monitoring equipment and sensors are specifically designed for, and built into, the system. Retro fit is an option but could be costly, especially if fitted to legacy equipment which may have a limited useful life remaining.
The use of these data-based systems will, no doubt, proliferate and continue to improve maintenance, efficiency and reduce costs in many ever increasingly complicated systems. Digital Twin systems could provide the ultimate predictive maintenance management tool, with total replication and representation of the physical equipment in cyberspace, with every parameter constantly monitored and assessed in real time throughout all life cycle stages.
For more information, please contact [email protected].
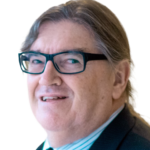
IMCA Contact
Andre Rose
Technical Adviser - Remote Systems and ROV, Offshore Survey, Digitalisation
Contact
Information Note Details
Published date: 30 November 2021
Information note ID: 1585
Downloads
IMCA’s store terms and conditions (https://www.imca-int.com/legal-notices/terms/) apply to all downloads from IMCA’s website, including this document.
IMCA makes every effort to ensure the accuracy and reliability of the data contained in the documents it publishes, but IMCA shall not be liable for any guidance and/or recommendation and/or statement herein contained. The information contained in this document does not fulfil or replace any individual’s or Member's legal, regulatory or other duties or obligations in respect of their operations. Individuals and Members remain solely responsible for the safe, lawful and proper conduct of their operations.