Exploring competence and safety
Published on 21 December 2021
It is impossible to consider safety in the workplace, without considering competence.
The United Kingdom Health and Safety Executive (HSE) website states:
“Competence can be described as the combination of training, skills, experience and knowledge that a person has and their ability to apply them to perform a task safely. Other factors, such as attitude and physical ability, can also affect someone’s competence.
As an employer, you should take account of the competence of relevant employees when you are conducting your risk assessments. This will help you decide what level of information, instruction, training and supervision you need to provide. Competence in Health and safety should be seen as an important component of workplace activities, not an add-on or afterthought.”
All tasks, in every working environment, require a risk assessment to be carried out and sufficient mitigations to be in place to reduce risk and ensure workers and the workplace are as safe as is reasonably possible. Each type of working environment has its own unique challenges and, to adequately identify potential hazards and levels of risk, requires a person who is experienced and competent in that particular area of operations.
It would be impractical to expect someone, who is experienced in office management, to carry out a risk assessment on a task being performed on the back deck of an offshore vessel for example. Clearly safety and specific task experience and competence are closely linked together, and it is imperative that the person carrying out the task risk assessment is experienced and competent in the subject matter.
In our working environments we strive to achieve “zero accidents”. This is a worthy, but difficult, goal to achieve, however, risk of accidents can be reduced by:
- Hazard Identification and Risk Assessments (HIRA)
- Task and Job Risk Assessments (TRA/JRA)
- Robust mitigation measures
- Safety Management and Operations Management processes
- Staff training, Continuous Professional Development (CPD) and Competence Management Systems (CMS) programmes
- Continuous Improvement programmes.
- Workforce engagement.
While adopting these measures has reduced the number of incidents, accidents, injuries and fatalities in the workplace, unforeseen events can still occur. Often the cause of these events may not be immediately obvious and may be the result of several factors combining to cause one catastrophic event.
When an incident or accident occurs there will be an in depth investigation carried out. The purpose of this investigation is to identify:
- Precisely what happened?
- How it happened?
- Why it happened?
- Could it have been prevented?
- How can it be prevented from re-occurring?
In many cases the root cause of an incident may well be attributed to a failure in the competence process, for example:
- A procedure not carried out correctly
- A misunderstanding or miscommunication of instructions
- A hazard or risk not correctly identified or mitigated against.
- A disregard of process due to time or cost savings
- Improper or inadequate training.
Even with equipment failure, competence is a consideration; was maintenance and inspection carried out correctly, were those completing the maintenance suitably competent?
Furthermore, human factors, at least in part, can impact competence such as:
- A momentary lapse of concentration
- A sudden distraction
- A pressing personal issue causing more prolonged distraction
- Pressure to achieve a deadline or completion of a task
- A wrong decision
- Advice not being heeded
To highlight this, here are some well-known accidents that were caused by competence failures at various levels.
Challenger Space Shuttle, Cape Canaveral, Florida.
On 28th January, 1986, seven astronauts died 73 seconds into the flight. Two O-ring seals located between adjacent segments of a booster rocket became displaced, due to severe cold weather, and allowed a hot flame to cut through a strut holding the main fuel tank. When the strut broke, the booster pierced the main tank and the shuttle exploded.
The Rogers commission report on the accident, cited NASA as being at fault for poor engineering and management practices. More disturbing was that a number of shuttle engineers had expressed concern over the unreliability of the O-rings two years before the accident, and had specifically warned of the potential danger given the extreme cold conditions the night before the flight. The commission identified a more fundamental problem in that NASA’s efforts to streamline shuttle operations in pursuit of its declared goal of flying 24 missions a year.
An article in the Space Safety Magazine states, “Blinded by the success of the early Shuttle flights, the Agency’s management had developed a careless attitude towards warnings coming from the engineering community. NASA had committed the Shuttle to an impossible schedule even before it entered in service in order to ensure funding. Over time, NASA management had grown increasingly impatient with the technical delays that operating such a complex machine required.”
The scheduled launch had been delayed for 6 days due to weather and technical problems, as a result, great pressure was felt to achieve this launch.
The commission concluded that, “The agency had simply been pushing too hard. The shuttle program had neither the personnel nor the spare parts to maintain such an ambitious flight rate without straining its physical resources or overworking its technicians.”
The Herald of Free Enterprise, Zeebruge, Belgium.
On 6th March, 1987, 193 people perished when rushed departures, in an effort to speed up service times, led to the ferry water-tight bow doors being shut after, rather than prior to, leaving port.
The assistant boatswain, failed to shut the doors and was sleeping in his cabin. The rest of the crew assumed the doors had been, or were being shut. The Captain assumed the doors were shut. The worst failure though, a request to install a warning device, costing only a few pounds, which would have given an indication on the bridge to show the door was closed had been denied by the company.
In the above accidents, it is clear to see that the competence of key personnel, at various levels, played significant roles in both of the disasters.
In the case of Challenger:
- Warnings, regarding the ability of the tank seals to perform adequately in cold weather, were ignored and left un-addressed when advised
- Poor decision making
- An unrealistic programme of launches, given the assets and engineering support available, causing unnecessary pressure to achieve the task.
- Management pressure to launch, in less than favourable conditions, to preserve image.
The pressure to achieve deadlines, in the case of the Herald of Free Enterprise, led to:
- Poor decisions being made
- Lack of, or poor, communication and assumptions on responsibility
- Responsibilities and duty being ignored
- Defined procedures being rushed or ignored
- Basic safety requirements being overlooked
- Complacency of the crew, since the system had been used and worked before.
- Management denying a cheap and simple solution that may have negated all the above problems.
As a final thought. The US Chemical Safety and Hazard Investigation Board (CSB) determines root causes of accidents, reports findings and issues recommendations for improvements. Although each incident they investigate is different, the CSB have identified the failure of management systems to adequately prevent incidents. The specific areas being:
- Lack of hazard review to predict and prevent incidents
- Insufficient investigation and follow-up after previous incidents
- Improper or inadequate training
- Failure to implement effective mechanical integrity programs
Competence of staff must be a priority to maintain a safe working environment.
Links to articles:
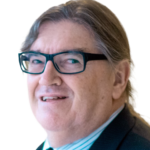
IMCA Contact
Andre Rose
Technical Adviser – Remote Systems and ROV, Offshore Survey, Digitalisation
Contact