Compressor fire
What happened?
There was a fire in a 25bar high flow diesel driven screw compressor installed on the back deck. The incident occurred on a diving support vessel operating within the 500m zone of a platform. The compressor was a long-term rental unit being used to provide ancillary air for subsea operations. It had had been running for 30 minutes at the time of the fire, and there were no indications of anomalies leading up to the incident. The fire was extinguished quickly and safely. There were no injuries.
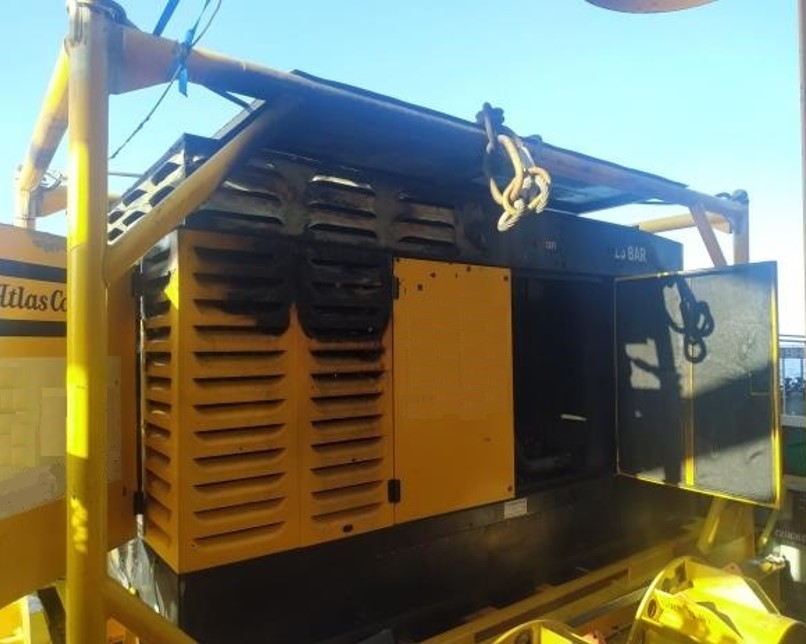
What went wrong?
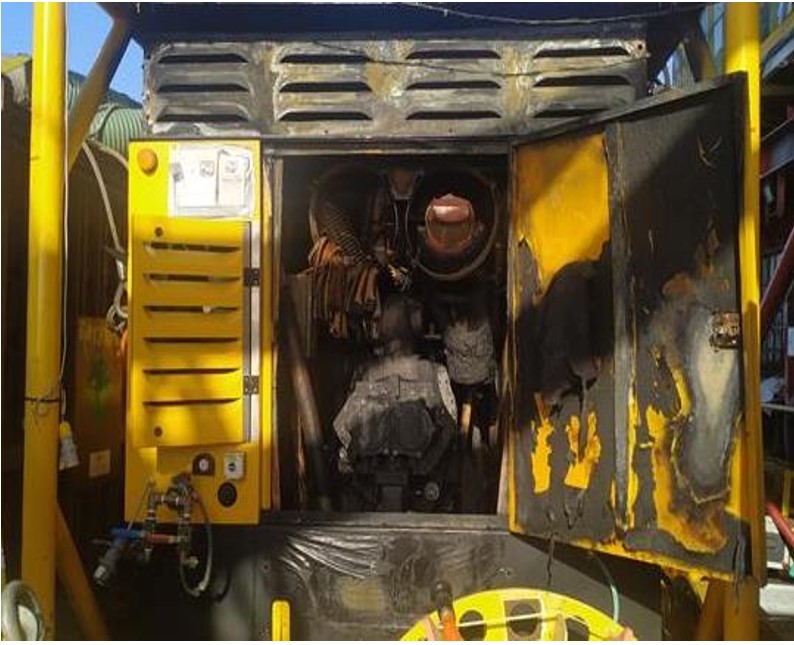
- There was a short circuit within the compressor electrical junction box, which melted insulation on cables both inside and outside the junction box;
- The radiant heat from the melted wires compromised the integrity of a nearby oil scavenger line;
- The scavenger line end fitting parted, which released compressor oil under pressure inside the compressor cabinet. This oil ignited, causing a fire which was fed by air being drawn across the compressor by the engine cooling fan.
Causal factors
- The Original equipment manufacturer (OEM) maintenance regime did not require the physical testing (i.e., insulation resistance checks) of wiring at each major service interval;
- The hired compressor was considered “standard equipment” within the company and did not require detailed pre-mobilisation inspection/surveillance activity;
- The risk assessment and management of change for the use of the compressor did not identify fire as a hazard associated with operating the equipment, and a safe use of work equipment assessment had not been completed.
Actions taken
- When procuring temporary equipment to be used in the offshore environment:
- Assess the potential fire hazard, and if applicable check the unit for in-built fire suppression capability and audible/visual alarm system set-up;
- Temporary equipment used in the offshore environment should be considered as non-standard, and procurement of such equipment should be subject to careful and appropriate checks;
- Before mobilizing mobile deck equipment onto vessels, consider the required inspection/surveillance necessary, inclusive of any run-up test and review of maintenance and operational history;
- Once temporary mobile deck equipment is mobilised, ensure that a safe use of work equipment assessment is completed;
- Deck plans should reflect the safe positioning of equipment and consider requirements for exclusion zones around adjacent equipment in event of fire.
Our member noted that this was the fourth compressor fire incident across their offshore operations since 2018.
Members may wish to refer to:
Safety Event
Published: 27 February 2023
Download: IMCA SF 06/23
IMCA Safety Flashes
Submit a Report
IMCA Safety Flashes summarise key safety matters and incidents, allowing lessons to be more easily learnt for the benefit of all. The effectiveness of the IMCA Safety Flash system depends on Members sharing information and so avoiding repeat incidents. Please consider adding [email protected] to your internal distribution list for safety alerts or manually submitting information on incidents you consider may be relevant. All information is anonymised or sanitised, as appropriate.
IMCA’s store terms and conditions (https://www.imca-int.com/legal-notices/terms/) apply to all downloads from IMCA’s website, including this document.
IMCA makes every effort to ensure the accuracy and reliability of the data contained in the documents it publishes, but IMCA shall not be liable for any guidance and/or recommendation and/or statement herein contained. The information contained in this document does not fulfil or replace any individual’s or Member's legal, regulatory or other duties or obligations in respect of their operations. Individuals and Members remain solely responsible for the safe, lawful and proper conduct of their operations.