Case Study – Common Power Supplies – Don’t have all your eggs in one basket
1 Overview
A vessel was conducting operations while operating in DP Follow Target Mode alongside a pipelayer. Unexpectedly, all six thrusters stopped functioning and were unavailable to DP Control. The vessel began to drift towards the pipelayer; however, after some time, two thrusters were activated in manual control and the vessel was able to avoid the pipelayer and manoeuvre into a safe position. The vessel eventually was able to recover all thrusters and return to DP Control.
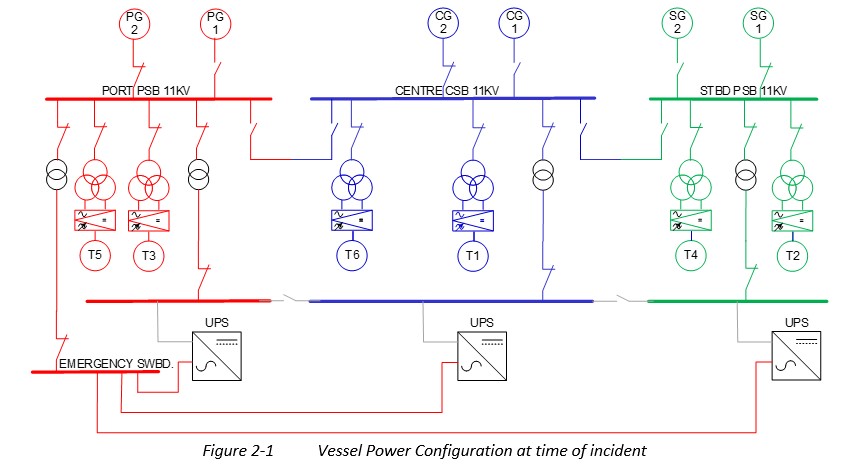
The switchboard was configured as a three-way split with one generator connected to each section, each section supplied power to two thrusters.
2 Cause
The underlying cause was the unintended closure of one of two rigsavers on one of the connected bus sections, which resulted in a loss of power and a reduction in speed on one engine, resulting in a decrease in frequency on the affected bus. In this instance, the affected bus supplied power to the emergency switchboard, which consequently experienced a reduction in frequency. During this time, the standby generator for the affected bus attempted to start and connect, but could not, due to the low frequency of the bus.
The three 440Vac switchboard UPS’s were supplied from the emergency switchboard; upon detecting the low frequency, these units sounded alarms on Inverter failure, triggering multiple communication alarms and causing the thrusters to de-select from DP Control and shut down. Finally, the affected generator tripped and locked out, initiating a blackout recovery on the affected bus; with normalised frequency levels, all thrusters were able to be recovered back into DP Control.
Note:
The RIG SAVER™ is a swing-gate, spring-operated, air-to-close, shut-off device mounted in the air intake system of the generator engine. The device uses stored energy by way of a spring to physically move the swing-gate into a closed position. Once the swing-gate is in the closed position it will latch. The RIG SAVER™ can only be reset (opened) locally with a 19mm wrench. Once activated it will impede the airflow into the cylinders and positively stop the engine. The RIG SAVER™ can be remotely operated (in this case using the engine start air) and/or locally by a pull toggle.
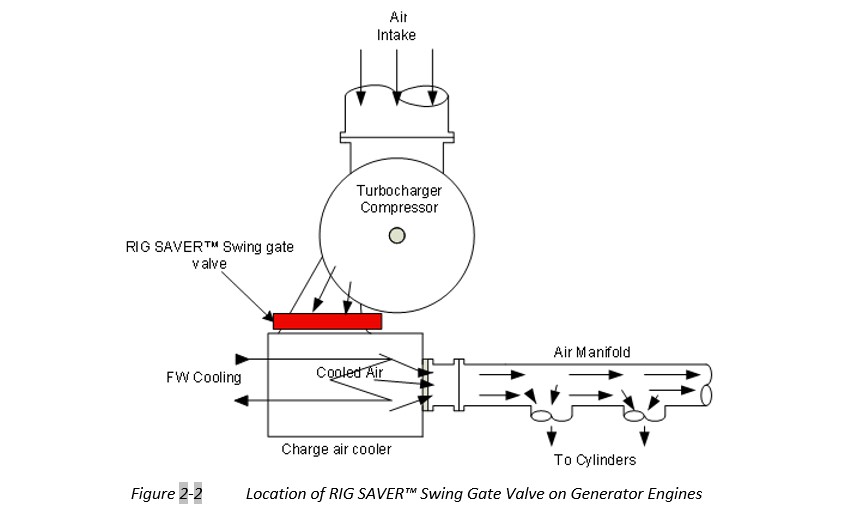
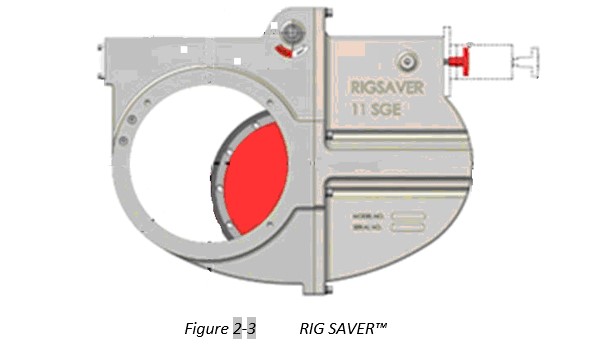
3 What can be concluded?
- A common failure caused the failure of all thrusters.
- Question: what is the normal operating configuration for the UPS’s?
- Should the Standard Operating Procedures (SOP) be that each UPS is fed by the individual LV switchboards? The feeder to the UPS from the emergency switchboard should only kick in during full black out, to keep the batteries charged.
4 Additional Comments
- Do not supply all your UPS units from the same switchboard, even if it is the Emergency Switchboard (ESB). This is a potential fault propagation path, and other types of voltage failures (such as over-voltage) could potentially be transferred as well.
- All ESB UPS unit power supply should have been identified as a concern in the FMEA and rectified accordingly during build and commissioning.
5 Guidance that would be relevant
The following IMCA Guidance would be relevant to this case study:
IMCA M220 – Guidance on operational activity planning
IMCA M103 – 2.12 (first part), 2.14, 2.7, 3.44, 3.5 and 3.7.
IMCA M117 – The training and experience of key DP personnel
IMCA M166 – Section 3.12 – Guidance on failure modes and effects analysis (FMEA)
IMCA M247 – Sections 2.5, 3.4 & 4.4.5 – Guidance to identify DP system components and their failure modes.
DP Event
Published: 29 June 2023
Download: IMCA DPE 02/23
Submit a Report
The following case studies and observations have been compiled from information received by IMCA. All vessel, client, and operational data has been removed from the narrative to ensure anonymity.
Case studies are not intended as guidance on the safe conduct of operations, but rather to assist vessel managers, DP operators and DP technical crew in appropriately determining how to safely conduct their own operations. Any queries should be directed to IMCA at [email protected]. Members and non-members alike are welcome to contact IMCA if they have experienced DP events which can be shared anonymously with the DP industry.
IMCA’s store terms and conditions (https://www.imca-int.com/legal-notices/terms/) apply to all downloads from IMCA’s website, including this document.
IMCA makes every effort to ensure the accuracy and reliability of the data contained in the documents it publishes, but IMCA shall not be liable for any guidance and/or recommendation and/or statement herein contained. The information contained in this document does not fulfil or replace any individual’s or Member's legal, regulatory or other duties or obligations in respect of their operations. Individuals and Members remain solely responsible for the safe, lawful and proper conduct of their operations.