Failure of proportional valve in saturation chamber control
What happened
There was a failure during saturation diving operations. There were no injuries to personnel nor damage to equipment, but time was lost. The automatic control system for the hyperbaric chamber detected that there was a proportional valve command/feedback discrepancy and stopped pressure control of the hyperbaric chamber. The valve malfunction forced an abort of diving operations and lost time.
What went right
- The PLC detected the discrepancy, isolated the line, alerted the operator in the control room and handed over control to the manual valve;
- The safety system designed to recover from the first failure worked effectively;
- The diving contractor involved, correctly decided to stop the diving activity, alerted the authorities, and started investigation sharing information with the saturation chamber suppliers and the valve manufacturer;
- The valve was correctly selected for the application, and had correct SIL2 certification.
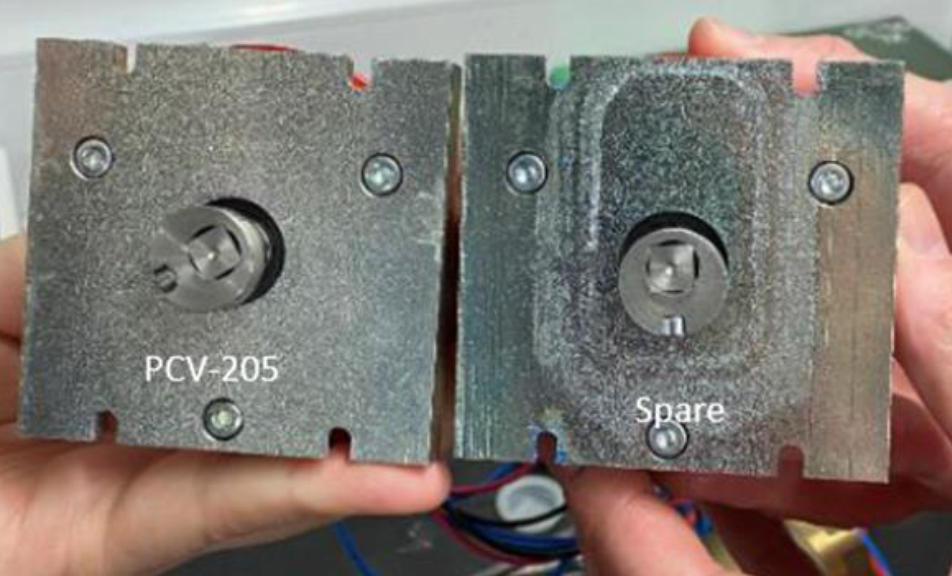
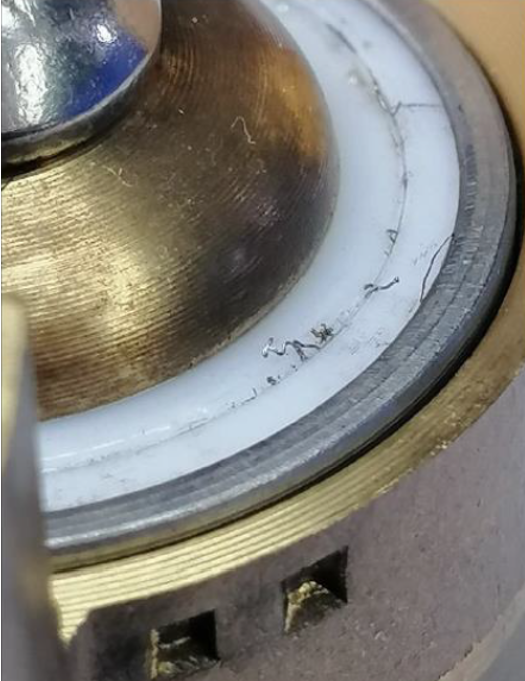
What went wrong
- The valve feedback did not respond correctly, the potentiometer was found defective;
- The diving contractor’s personnel had dismantled the valve (although this was prohibited by the manufacturer) in an attempt to solve the problem. It had to be reassembled 180° upside down because the drive shaft was out of alignment with its ‘set’ zero point. This made it impossible to understand if the potentiometer was damaged by wear of time or by wrong disassembly/assembly;
- Investigation found debris in the valve seat, which could have led to more serious problems (see second image).
Lessons
- Manufacturers recommended maintenance should be followed. If operational experience falls outside this, the OEM should always be consulted with a view to ensuring manuals are updated and knowledge shared;
- Work with manufacturers and suppliers to ensure there are up-to-date maintenance procedures;
- Follow an equipment supplier’s recommendation for critical spares;
- Ensure personnel are properly trained to operate safety critical equipment in all circumstances.
Actions
- Share incident with operators of similar saturation systems equipped with that specific equipment;
- Ensure there is a stock of spares considered critical by the saturation system supplier;
- Amend planned maintenance system to include appropriate testing, maintenance or planned replacement of critical parts;
- The supplier of the saturation system further recommended:
- Checking pipe cleaning status and filtering throughout the system;
- Ship all dismantled valves to the manufacturer for further examination;
- Perform appropriate tests before returning to dive operations.
Members may wish to refer to:
- Uncontrolled movement of A-frame [failure of proportional valve driver]
- Loss of redundancy in diving bell launch and recovery (LARS) PLC system
Safety Event
Published: 27 November 2023
Download: IMCA SF 27/23
IMCA Safety Flashes
Submit a Report
IMCA Safety Flashes summarise key safety matters and incidents, allowing lessons to be more easily learnt for the benefit of all. The effectiveness of the IMCA Safety Flash system depends on Members sharing information and so avoiding repeat incidents. Please consider adding safetyreports@imca-int.com to your internal distribution list for safety alerts or manually submitting information on incidents you consider may be relevant. All information is anonymised or sanitised, as appropriate.
IMCA’s store terms and conditions (https://www.imca-int.com/legal-notices/terms/) apply to all downloads from IMCA’s website, including this document.
IMCA makes every effort to ensure the accuracy and reliability of the data contained in the documents it publishes, but IMCA shall not be liable for any guidance and/or recommendation and/or statement herein contained. The information contained in this document does not fulfil or replace any individual’s or Member's legal, regulatory or other duties or obligations in respect of their operations. Individuals and Members remain solely responsible for the safe, lawful and proper conduct of their operations.