Failure of pallet lifters
A member has reported two incidents involving the failure of pallet lifters. The first incident resulted in the failure of a wire rope for a fork pallet lifter which parted following the lifting of a load of chemical drums onto a vessel deck. The second incident resulted in a pallet lifter fork being twisted due to overloading during a lifting operation to load a pallet of steel plate onto a vessel deck.
Incident 1
A pallet lifter with a 2.5T safe working load (SWL) had lifted a 400kg load of 16 chemical drums onto the working deck of a vessel. The chemical drums being lifted had also been cargo strapped to the lifter as a means of secondary securing. The pallet lifter in use had recently undergone a thorough inspection and had been correctly colour-coded by a 3rd party inspection company to verify its fitness for purpose. As the load was landed on the deck, a rigger removed the lifter forks from the pallet. At this point the wire rope (which attaches to the lifting eye and the tensioning springs on this particular model) parted and the wire struck the rigger across the back of his hand. There were no injuries as the rigger was wearing Kevlar gloves which provided adequate protection for this type of operation. The rigger notified the vessel supervision and the pallet lifter was taken out of use immediately.
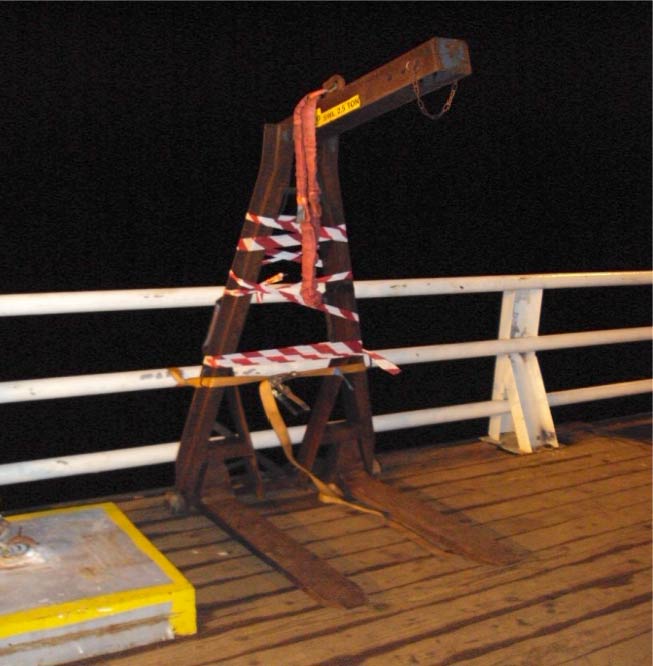
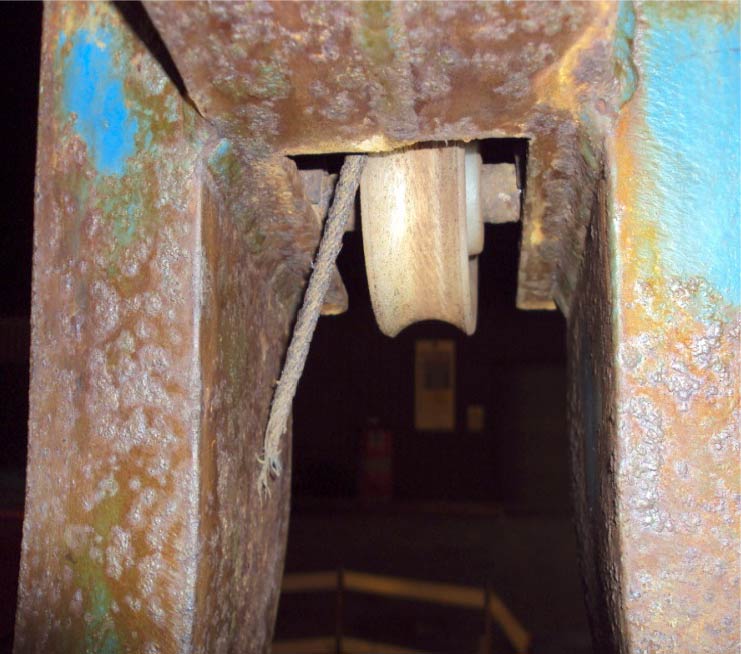
After investigation, the following was:
- On further inspection, the general condition of the pallet lifter, and the wire rope in particular were found to be in poor condition and showing signs of corrosion and poor maintenance. This should have been noticed;
- The 3rd party inspection company which had completed a thorough inspection of the lifter to allow its updated colour-code and continued use had clearly not provided a sufficient standard of inspection to ensure this piece of equipment was safe for work on this vessel;
- All lifting equipment should be given a full visual inspection by the user prior to any lifts, with all defects or concerns being raised immediately. The condition of this lifter should have been noticed and highlighted by the onboard team;
- There was no on-going maintenance on this kind of equipment and they are used until failure;
- Had the pallet lifter been entered into the vessel planned maintenance system this would allow for regular inspections to take place, with paint and greasing regimes to be implemented as necessary;
- When purchasing lifting equipment for vessel use, full consideration should be given by a competent person as to whether or not the item is suitable for the operations and environment in which it will be used onboard.
Incident 2
A pallet lifter with a 2.0T SWL was being used to transfer pallets of steel plate on to the main working deck of a vessel. The plate being loaded was delivered on pallets and wrapped with plastic covers. The weight of the load had not been provided by the supplier and was not known to the lifting team prior to the lift.
This lifting operation involved inserting the pallet lifter forks, and the load being raised slightly to allow a secondary cargo strap to be positioned around the load and prevent any movement during the lift. However, as the load was raised approximately six inches off the quayside to attach the cargo straps, the plates moved, sliding forward and to the left of the forks. The pallet lifter and load was then returned to the quay and the forks removed from the pallet. Once the pallet lifter had been removed from the pallet it was evident that the left fork had been twisted due to the load moving and overloading the pallet lifter fork.
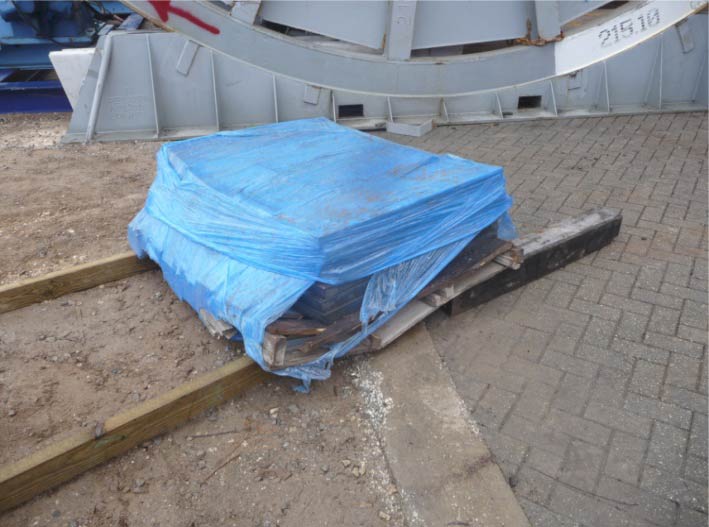
After investigation, the following was noted:
- A permit to work and lift plan had been completed for this operation but no consideration was given to the lack of information about the load to be moved or the limitations of the pallet lifter. This should have been highlighted in the lift plan risk assessment and the toolbox talk prior to moving the pallets. Hazard awareness and correct lifting procedures were not applied during this lifting operation;
- As the steel plate loads had no clear indication of the weights contained on each pallet, a lifter which has a SWL of 2.0T should not have been used without confirmation that the working limits would not be exceeded by the load;
- Good practice for transporting of plate onto vessels should be to transfer the load into a certified lifting basket ensuring the lifting of all plates in a contained and controlled manner.
Safety Event
Published: 23 December 2011
Download: IMCA SF 14/11
IMCA Safety Flashes
Submit a Report
IMCA Safety Flashes summarise key safety matters and incidents, allowing lessons to be more easily learnt for the benefit of all. The effectiveness of the IMCA Safety Flash system depends on Members sharing information and so avoiding repeat incidents. Please consider adding [email protected] to your internal distribution list for safety alerts or manually submitting information on incidents you consider may be relevant. All information is anonymised or sanitised, as appropriate.
IMCA’s store terms and conditions (https://www.imca-int.com/legal-notices/terms/) apply to all downloads from IMCA’s website, including this document.
IMCA makes every effort to ensure the accuracy and reliability of the data contained in the documents it publishes, but IMCA shall not be liable for any guidance and/or recommendation and/or statement herein contained. The information contained in this document does not fulfil or replace any individual’s or Member's legal, regulatory or other duties or obligations in respect of their operations. Individuals and Members remain solely responsible for the safe, lawful and proper conduct of their operations.