High potential near-miss during equipment testing
A member has reported an incident in which a heavy metal work table was dragged nearly a metre by a forklift truck. The incident occurred during troubleshooting of a heavy duty multi-strand electrical cable. Technicians connected the cable between a metal worktable vice and the rear towing / pull pin of a forklift truck, in order to allow stretching and tensioning of the cable. Once the stretched cable was tested, the tension was released and the forklift truck shut down. The cable was not disconnected from either the worktable vice or the forklift. A short time later, another employee boarded the forklift truck, started the engine and began to drive away. The cable jerked taught and pulled the metal worktable forward approximately 1m before warning shouts were recognized and the forklift was stopped.
No personnel were injured and no equipment was damaged. However, the potential for personnel to have been injured and equipment to have been damaged was very high had personnel been at the work table or had the work table been pulled over. At the time of the incident there were a number of costly pieces of electronic equipment on the work bench.
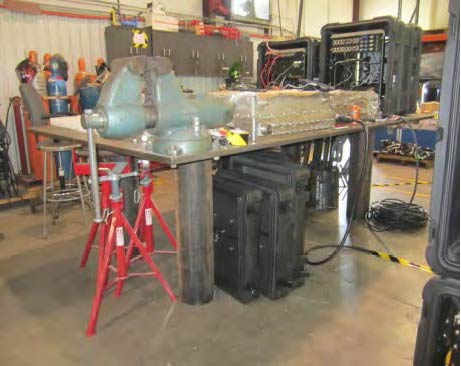
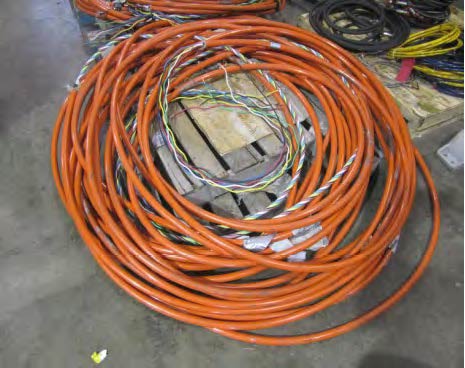
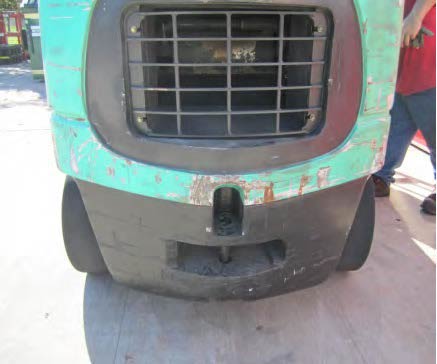
The company’s investigation revealed the following:
- There were no test procedures for the set-up and use of the forklift for stretching and tensioning the cable;
- There was no job safety analysis (JSA) addressing actual or potential hazards of stretching and tensioning the cable with the forklift in order to support troubleshooting of the electrical cable;
- The electrical cable had not been removed from either the worktable vice or the forklift once the tensioning had been completed;
- There was inadequate communications between employees – no communication took place between the personnel using the forklift for testing and the operator who sought to drive the forklift from the area;
- The operator who boarded the forklift did not inspect or walk around the vehicle before starting up and driving away;
- There were inadequate guards or barriers – the forklift had not been secured to prevent access (i.e., no warning signs, labels, the key had not been removed from the ignition, etc.);
- The testing of the cable was rushed to completion without a thorough review of all aspects of equipment, personnel and process.
Further investigation revealed the following root causes:
- Inadequate leadership/supervision – Proper management of the overall testing process, equipment, and personnel would have prevented this near miss incident. Contributing factors to this root cause include inadequate work planning, inadequate identification and evaluation of the potential loss/hazards/risks, and inadequate or missing documentation (JSA, procedures, and/or instructions, etc.) which would have provided better control of work;
- Poor communication between peers – No communications took place between the operator and the using department before the operator started the forklift and drove away;
- Improper motivation – The failure of the operator to visually check the status of the forklift prior to use demonstrated complacency with the dangers and hazards of forklift operations.
Our member took the following actions:
- Testing methods, especially when unique or uncommon, should be documented and a Job Safety Analysis performed to ensure all hazards and risks are identified, understood and mitigated against;
- Controls for equipment, personnel and process should be planned, defined and monitored for compliance by assigned, responsible personnel;
- Ensured that improved communication processes were established and maintained to prevent recurrence of same or similar incidents;
- Continued to reinforce safety protocols, practices and behaviours with all personnel to overcome complacency to work place hazards.
Safety Event
Published: 4 April 2013
Download: IMCA SF 05/13
IMCA Safety Flashes
Submit a Report
IMCA Safety Flashes summarise key safety matters and incidents, allowing lessons to be more easily learnt for the benefit of all. The effectiveness of the IMCA Safety Flash system depends on Members sharing information and so avoiding repeat incidents. Please consider adding [email protected] to your internal distribution list for safety alerts or manually submitting information on incidents you consider may be relevant. All information is anonymised or sanitised, as appropriate.
IMCA’s store terms and conditions (https://www.imca-int.com/legal-notices/terms/) apply to all downloads from IMCA’s website, including this document.
IMCA makes every effort to ensure the accuracy and reliability of the data contained in the documents it publishes, but IMCA shall not be liable for any guidance and/or recommendation and/or statement herein contained. The information contained in this document does not fulfil or replace any individual’s or Member's legal, regulatory or other duties or obligations in respect of their operations. Individuals and Members remain solely responsible for the safe, lawful and proper conduct of their operations.