Near-miss: Broken chain on sling of personnel lifting basket
A member has reported a near miss incident in which a chain link snapped under load. The incident occurred during a six monthly on-board lifting and rigging inspection. A deck foreman was required to arrange the lifting of an empty personnel basket from one place to another on the vessel. The basket was connected to the crane block, the deck foreman gave the command to lift, and as soon as the crane took up the full load of the basket, one of the chain links from the main chain sling of the basket snapped. There were no injuries.
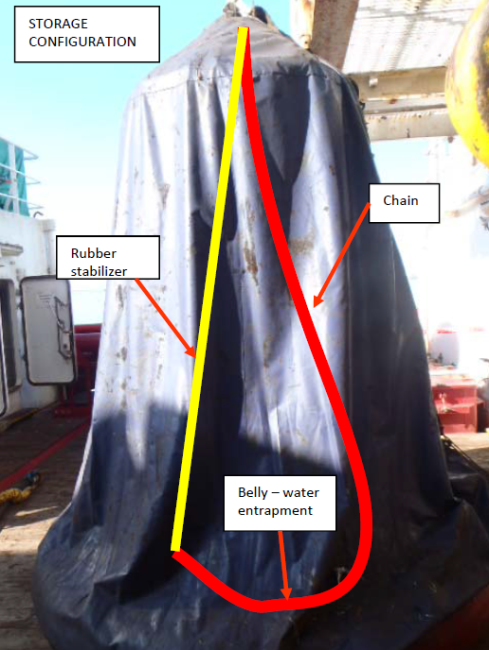
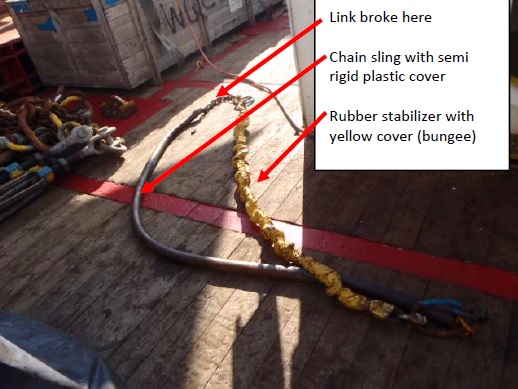
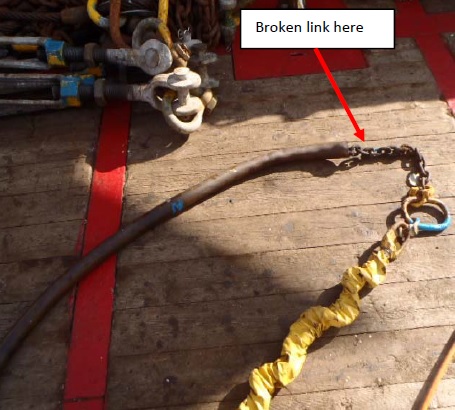
Our member’s investigation revealed the following:
- The configuration of the rigging (the ‘bungee’ was shorter than the chain) created a space or belly during storage, with water trapped inside the plastic cover around the chain. Accelerated corrosion occurred, which may have contributed to chain failure. Corrosion, shock load and/or chain manufacturing process are potential causes for rigging failure;
- The sub-contractor doing the rigging inspection was not accredited by the manufacturer of the personnel basket to conduct inspections of such baskets. The internal procedure they used was a for steel-made work basket, and hence not applicable to a personnel basket;
- The last load test on this particular rigging and basket had been performed eighteen months before, whereas the load test should have taken place every sixth month as per manufacturer recommendation;
- The inspection company did not remove the plastic protection cover to inspect the chain, which meant that the visual inspection was not complete.
Our member took the following actions:
- Removed protection cover from rigging and performed thorough visual inspection;
- Checked that the storage configuration of the rigging does not allow water entrapment and associated corrosion;
- Investigated the possibility of replacing the plastic protection cover by an easy-to-remove cover type, for easier inspection;
- Checked personnel basket user manual and reviewed if rigging inspection sub-contractor was meeting manufacturer recommendations during last recertification campaign.
Members may wish to refer to the following similar incidents (key words: corrosion, failure):
Safety Event
Published: 10 August 2015
Download: IMCA SF 11/15
IMCA Safety Flashes
Submit a Report
IMCA Safety Flashes summarise key safety matters and incidents, allowing lessons to be more easily learnt for the benefit of all. The effectiveness of the IMCA Safety Flash system depends on Members sharing information and so avoiding repeat incidents. Please consider adding [email protected] to your internal distribution list for safety alerts or manually submitting information on incidents you consider may be relevant. All information is anonymised or sanitised, as appropriate.
IMCA’s store terms and conditions (https://www.imca-int.com/legal-notices/terms/) apply to all downloads from IMCA’s website, including this document.
IMCA makes every effort to ensure the accuracy and reliability of the data contained in the documents it publishes, but IMCA shall not be liable for any guidance and/or recommendation and/or statement herein contained. The information contained in this document does not fulfil or replace any individual’s or Member's legal, regulatory or other duties or obligations in respect of their operations. Individuals and Members remain solely responsible for the safe, lawful and proper conduct of their operations.