Near-miss: Dropped torque tool
A member has reported an incident in which a torque tool, weighing 55 kg, was dropped back into the sea during recovery after use by divers, who were working below. The incident occurred after the tool had been lowered to the seabed for valve functioning work by the divers. The deployment and recovery of the torque tool was conducted using the small crane (cherry picker) in a tandem lift with the winch and power sheave for the hydraulic hoses. These remained attached throughout this process.
The torque tool had various items retrofitted to it by the supplier, including a protection frame and two 25mm lifting eyebolts. The eyebolts were poorly located, impacting heavily on the component parts and only one was certified for lifting. The tool was provided to the vessel without rigging or guidance as to how it should be lifted.
The lift was incorrectly categorised as ‘straightforward’. It was covered under the generic toolbox talk and no lift plan was created. The rigging arrangement decided upon was a ‘basket hitch lift’ using a 1Te webbing sling which was ‘snaked’ through the uncertified protection frame. This rigging arrangement was not communicated to the diver, who assumed the webbing sling was choked on itself. He re-applied the sling using a single lifting eye only.
On recovery, as the torque tool cleared the ‘splash zone’, the webbing sling released and the tool fell back into the water. A ‘freefall’ of the tool was only prevented by the attached hydraulic hoses, through which the tool was successfully recovered to deck.
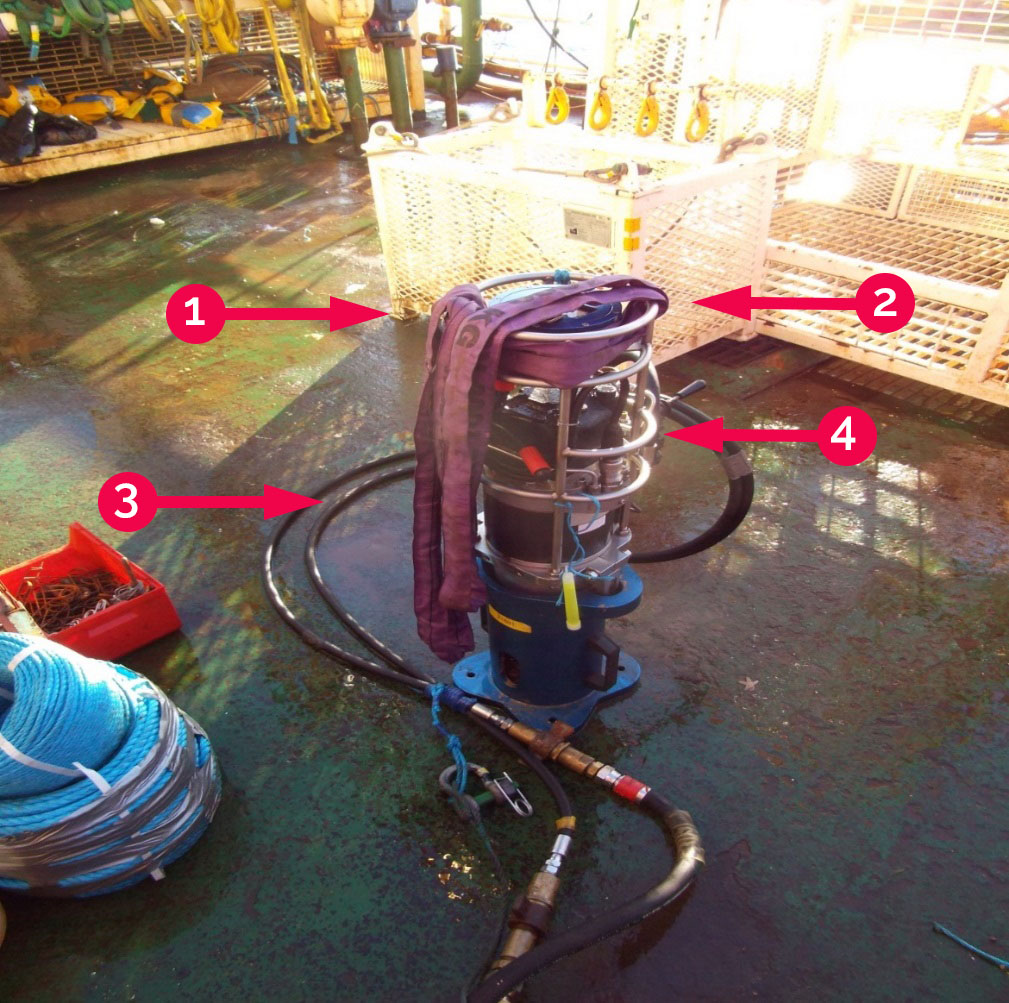
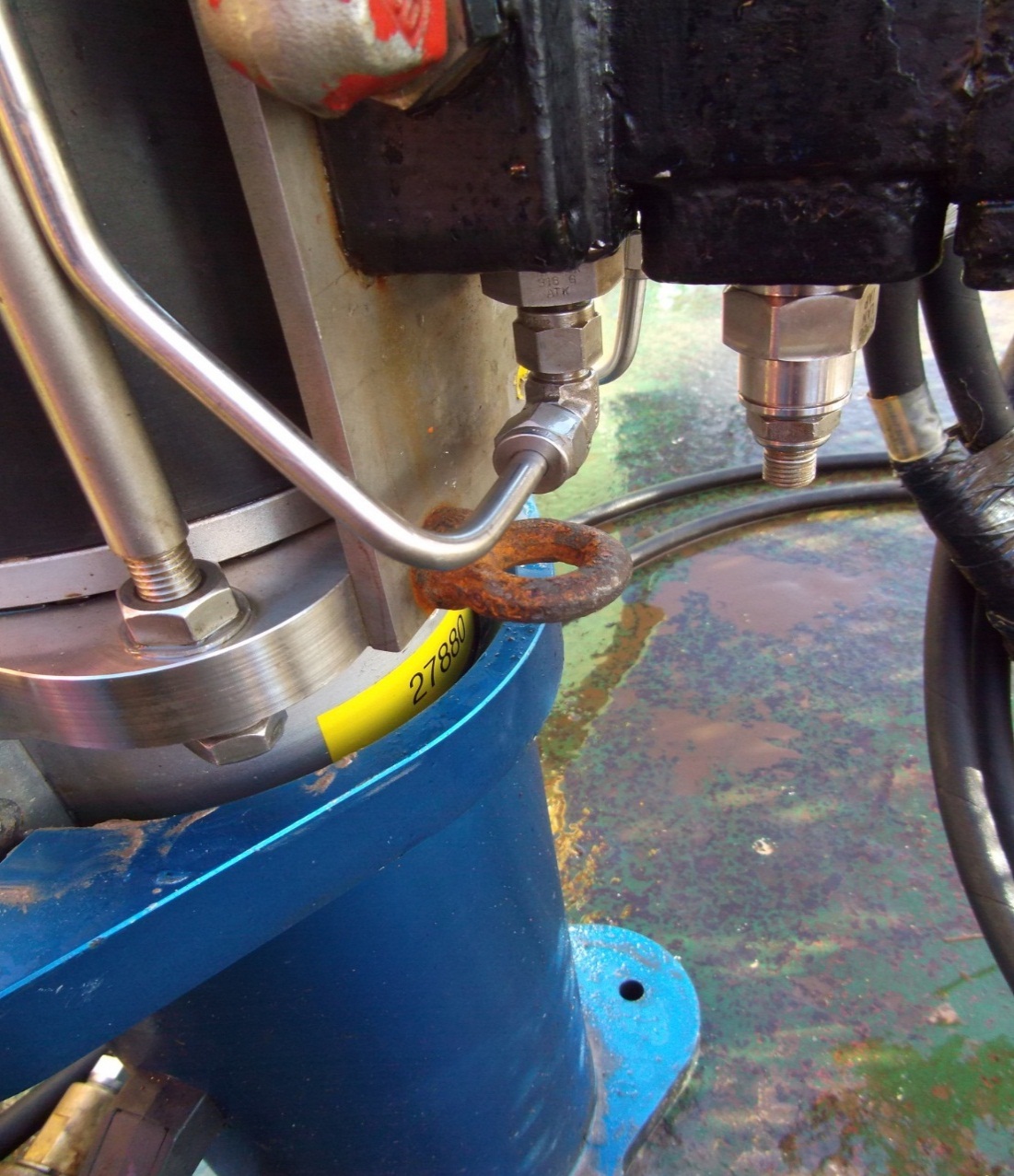
Our member noted the following:
- Risk assessment was inadequate;
- There was a failure to comply with existing company lifting procedures and guidance. This led to incorrect lift categorisation and a failure to create a lift plan;
- Manuals from the supplier were out of date and contained no information or guidance on how the tool was to be rigged for subsea deployment;
- The torque tool was deficient in suitable and certified lifting points, but was accepted and presented for use on board the vessel. These deficiencies were sufficient for the tool to have been rejected at the time of inspection;
- A diver and unprotected subsea assets were present within the potential DROPS cone radius of 36m. Safe distances and locations for divers should be identified and complied with before lifting operations start;
- Rigging and lifting certification is not currently a core requirement for divers at this company. A review of diver related lifting operations training is being conducted to establish the rigging and lifting competency of those involved in this process.
Our member concluded the following:
- Immediate cause:
- The incorrect re-attachment of the rigging subsea. This was a human error brought about by various contributory factors, including the failure to communicate the rigging arrangement to the diver
- The torque tool was supplied to the vessel with one certified lifting point and no suitable rigging nor lift plan defining how the deployment and recovery should be conducted.
Our member recommended:
- A review of operations to identify similar circumstances where equipment is being lifting using uncertified lifting points or where there is a failure to comply with existing lifting procedures; . Ensuring that suitable lifting points and lift plans are available; . Ensuring that appropriate guidelines, procedures and information are communicated to all personnel involved.
Members may wish to refer to the following incidents (search words: subsea, lifting, near miss, cone):
Please also consult Guidelines for lifting operations.
Safety Event
Published: 13 April 2016
Download: IMCA SF 08/16
IMCA Safety Flashes
Submit a Report
IMCA Safety Flashes summarise key safety matters and incidents, allowing lessons to be more easily learnt for the benefit of all. The effectiveness of the IMCA Safety Flash system depends on Members sharing information and so avoiding repeat incidents. Please consider adding [email protected] to your internal distribution list for safety alerts or manually submitting information on incidents you consider may be relevant. All information is anonymised or sanitised, as appropriate.
IMCA’s store terms and conditions (https://www.imca-int.com/legal-notices/terms/) apply to all downloads from IMCA’s website, including this document.
IMCA makes every effort to ensure the accuracy and reliability of the data contained in the documents it publishes, but IMCA shall not be liable for any guidance and/or recommendation and/or statement herein contained. The information contained in this document does not fulfil or replace any individual’s or Member's legal, regulatory or other duties or obligations in respect of their operations. Individuals and Members remain solely responsible for the safe, lawful and proper conduct of their operations.