Crewman struck and injured by forklift truck
A member has reported an incident in which a person was struck by a shipyard forklift while returning to the vessel from the yard machine shop. The blow to the leg resulted in him spinning and falling across the forks, striking his right shoulder and hip and dislodging his hard hat and safety glasses. The operator stopped the machine as the person was falling across the forks. He exited the forklift to attend and see if there were any injuries. At that time, it was determined that there were no injuries sustained from the incident and the person returned to the vessel.
It was later noted that the injured person was not looking well. He was advised to proceed to the hospital for a precautionary check-up. Tests and X-rays did not reveal any broken bones or internal injuries. He nevertheless later started to develop pain in his shoulder and hip which had not subsided in the following weeks. After following up with his family doctor he was placed on restricted work.
This incident was captured on the shipyard’s security camera. A request was made to obtain a video copy or time lapse screen shots. This was not permitted by the yard management. However, unlimited visual access was permitted to review the footage.
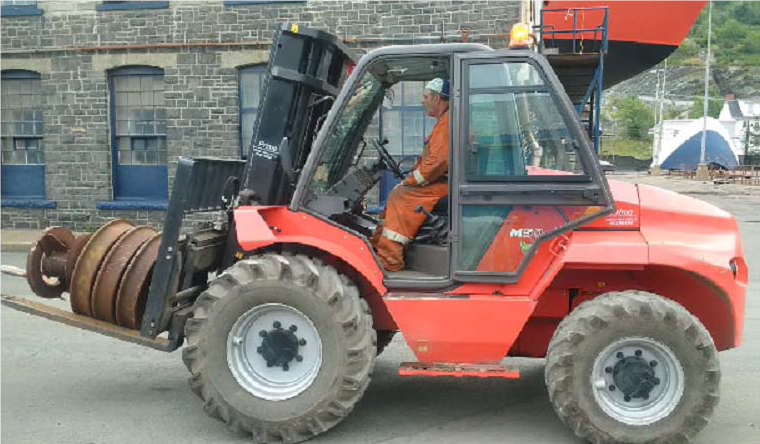
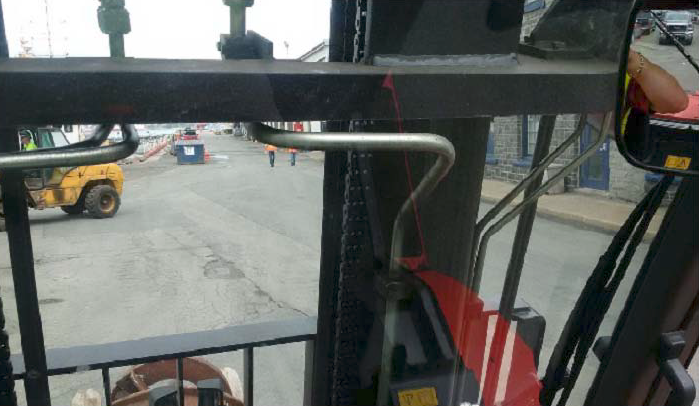
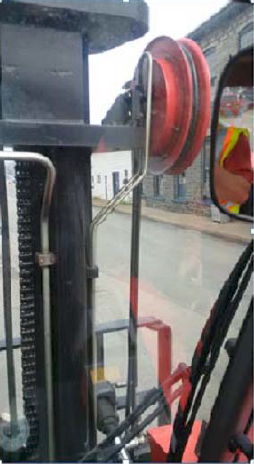
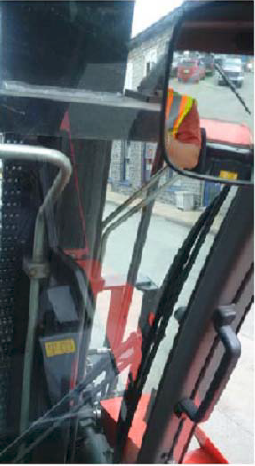
Our members’ investigation revealed the following:
- The forklift operator reported that:
- he did not see the injured person because of blind spots due to the design equipment
- the blind spots were larger on this model of forklift than on other models in use at the yard;
- The injured person stated that he did not see the forklift until the impact. This was apparent from review of the video footage which confirmed that there was no change in his direction, body movement or speed up to the time of impact;
- The forklift was approaching from a slight angle behind the injured person’s immediate left which may have been out his peripheral vision and a contributory factor in the incident;
- The forklift made a slight adjustment of direction to the right due to a truck parked next to the main building. This may have put the injured person into the blind spot of the forklift;
- At the time of the incident the forklift was not carrying any load;
- It was not possible to tell from the video whether or not the speed of the forklift was a contributory factor;
- At the time of the incident all personal protective equipment (PPE) was being worn by the injured person as required, including “hi-viz” vest;
- The location of the incident was in an open section of the yard with good visibility all around. There were no objects, fixtures or buildings between the forklift operator and the injured person;
- There were no dedicated walkways around the shipyard with the exception of inside the machine shop.
Our member concluded that the immediate causes were:
- Incorrect use of machinery or equipment:
- the forklift operator was aware that the equipment had blind spots and failed to monitor and check these;
- Failure to follow rules and regulations:
- local rules required that crew members “must be aware of mobile machinery such as cranes, forklifts and manlifts”
- there was no traffic management within the yard with regards to the travelling of mobile equipment. Workers were able to transit the yard at any angle in any direction leaving the equipment operator vulnerable to an incident. CSA B335-15 states “All efforts shall be made to keep pedestrians separate from powered lift trucks.”
“Basic” causes identified included:
- Routine, monotony, demand for uneventful vigilance:
- the work of the injured person consisted of many visits to the yard workshop from the vessel; it was evident that complacency played a part in the incident. It would also be expected that the forklift operator would have been able to identify the injured person crossing the yard from the workshop;
- Inadequate identification and evaluation of loss exposures:
- while this hazard has been identified in the workshop/machine shops where walkways are painted in place, it was not identified outside in the open yard;
- Inadequate consideration of human factors/ergonomics:
- the design of the forklift cab did not allow for a clear wide angle view from the operator position. This was also mentioned by the operator during his first time operating the equipment.
Corrective actions taken (other than medical treatment and circulation of this incident):
- Shipyard to review CSA B335-15 Safety Standard for Lift Trucks Section 4.5.5.2 (Traffic Management) and adopt the recommendations made;
- Though it could not be determined that speed was a factor, limit the speed of the yard forklifts and other machinery to a maximum of 15km/hr;
- Recommend the shipyard release a bulletin highlighting the incident and inviting suggestions for improvement from their workforce.
Members may wish to review Guidance on safety in shipyards
Members may also wish to refer to the following incident:
Safety Event
Published: 27 February 2017
Download: IMCA SF 04/17
IMCA Safety Flashes
Submit a Report
IMCA Safety Flashes summarise key safety matters and incidents, allowing lessons to be more easily learnt for the benefit of all. The effectiveness of the IMCA Safety Flash system depends on Members sharing information and so avoiding repeat incidents. Please consider adding [email protected] to your internal distribution list for safety alerts or manually submitting information on incidents you consider may be relevant. All information is anonymised or sanitised, as appropriate.
IMCA’s store terms and conditions (https://www.imca-int.com/legal-notices/terms/) apply to all downloads from IMCA’s website, including this document.
IMCA makes every effort to ensure the accuracy and reliability of the data contained in the documents it publishes, but IMCA shall not be liable for any guidance and/or recommendation and/or statement herein contained. The information contained in this document does not fulfil or replace any individual’s or Member's legal, regulatory or other duties or obligations in respect of their operations. Individuals and Members remain solely responsible for the safe, lawful and proper conduct of their operations.