Failure of hose reel bearing housing
A member has reported a serious failure of a shaft bearing housing on a hydraulic winch rented from a third-party contractor. During recovery of a load from the seabed, the shaft bearing housing broke. The winch wire raced out 2-3 metres before the drum got stuck in the casing and stopped rotating. The ‘fail-safe’ brakes of the winch did not engage when the drum became misaligned. The winch was certified to SWL (safe working load) 17 Te, while the load at the time of the incident was approximately 8 Te. There were no injuries.
During the company’s investigation the following points were noted:
- A laboratory test revealed that the winch had been exposed to repetitive overload prior to being taken onboard the company’s vessel, causing cracks in the bearing housing to develop over time;
- During preparation of the winch prior to mobilisation on the vessel, the certification body required a reinforcement of the winch frame at the motor side. This could have been an indication that the winch frame had been sagging at the motor side (where the bearing housing broke) which may have contributed to the damage;
- The winch was ostensibly certified to DNV Rules for Certification of Lifting Appliances, 1994. However, a review of the design documentation for the winch and bearing/housing compared with this certification revealed that the winch assembly was not compliant in several areas:
- with a winch SWL of 17 Te, calculations carried out by the engineering team showed that the breaking load of the bearing housing should be 76 Te according to the DNV Rules for Certification of Lifting Appliances 1994
- the design calculations initially carried out by the winch manufacturer were based on a load angle of 0-30°. Within this area the breaking load of the bearing housing is 79 Te. The winch had later been fitted with a spooling device changing the load angle to 120-150° but no new design calculations were carried out for the new setup/angle. The datasheet for the bearing/housing stated that the breaking load at this angle was reduced to 32-35 Te, less than half of what is required for the SWL to which the winch was certified
- this winch does not have a secondary band brake, but only brakes from the hydraulic transmission system.
- the calculations also showed the brake capacity was too low for the indicated SWL of the winch. DNV Lifting Appliances 1994 Section 5 B307 states that minimum brake capacity is to be 80% in excess of SWL, i.e. 17×1.8=30.6 Te, while the braking capacity of this winch was defined to be 25.5 Te
- during a complete refurbishment of the winch in 2006 the same bearing with housing was replaced due to cracks and damage on the housing. No investigation was done into why or how this damage had developed;
- If the winch, with the spooling device fitted, had been exposed to loads up to its SWL and additionally been load tested to SWL x 1.1, this would have significantly increased the risk of damaging the shaft bearing housings and explains the low cycle fatigue damage of the axle bearing housings;
- Further, as no non-destructive testing (NDT) was carried out on the winch bearing housings and the visual check did not reveal any damage, it was not possible to identify the cracks during mobilisation preparations.
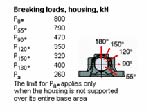
Based on these findings it was found to be clear that this winch was not suitable to be used to a safe working load of 17 Te. However, without regular NDT of winch bearings and other load bearing parts on winches, this could have happened to basically any winch in operation, especially when any modifications have taken place.
The company suggested the following actions:
- Establish procedures for NDT of all load bearing parts as part of ‘routine’ maintenance and/or mobilisation checks for winches and other lifting appliances;
- Consider failure mode and effects analysis(FMEA)/criticality analysis for all such equipment, addressing single failure points such as bearings and brakes;
- Consider whether NDT is sufficient to find defects if secondary braking is in place;
- Ensure that winches and other lifting appliances fulfil the requirements of the rules and standards to which they were designed and certified. If the design basis has changed, for example, by changing the wire angle, ensure that design calculations consider the new scenario;
- For future lifting operations the company recommended that such winches should not be used without a proper drum disk brake, since there was no proper second barrier for safety. This was also noted to be the recommendation in the DNV lifting Appliances Rules section 5 B306.
- Members may also refer to Guidelines for lifting operations for further assistance and information on lifting.
Safety Event
Published: 8 April 2010
Download: IMCA SF 02/10
IMCA Safety Flashes
Submit a Report
IMCA Safety Flashes summarise key safety matters and incidents, allowing lessons to be more easily learnt for the benefit of all. The effectiveness of the IMCA Safety Flash system depends on Members sharing information and so avoiding repeat incidents. Please consider adding [email protected] to your internal distribution list for safety alerts or manually submitting information on incidents you consider may be relevant. All information is anonymised or sanitised, as appropriate.
IMCA’s store terms and conditions (https://www.imca-int.com/legal-notices/terms/) apply to all downloads from IMCA’s website, including this document.
IMCA makes every effort to ensure the accuracy and reliability of the data contained in the documents it publishes, but IMCA shall not be liable for any guidance and/or recommendation and/or statement herein contained. The information contained in this document does not fulfil or replace any individual’s or Member's legal, regulatory or other duties or obligations in respect of their operations. Individuals and Members remain solely responsible for the safe, lawful and proper conduct of their operations.