High potential DROPS near miss: failed crane component
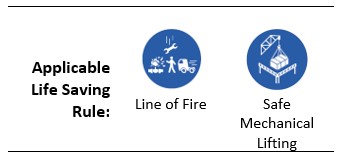
What happened?
Whilst preparing a crane for operations, the additional man riding calliper brake casing cover on the primary winch failed, causing the brake pad, rings and cover to fall to the deck along with a small discharge of hydraulic oil.
Five items were found on the deck below, these would have dropped from a height of about 25m. Two of the largest items dented the wooden sheathing to a depth of 1 – 3 mm. One of these weighed 1100g, the other, 460 g. The remaining three items left no indents.
The casing cover was not found and was presumed to have fallen into the sea during the failure.
There were no crew nearby at the time and there were no injuries. The dropsonline.org calculator indicates this could potentially have resulted in a fatality.
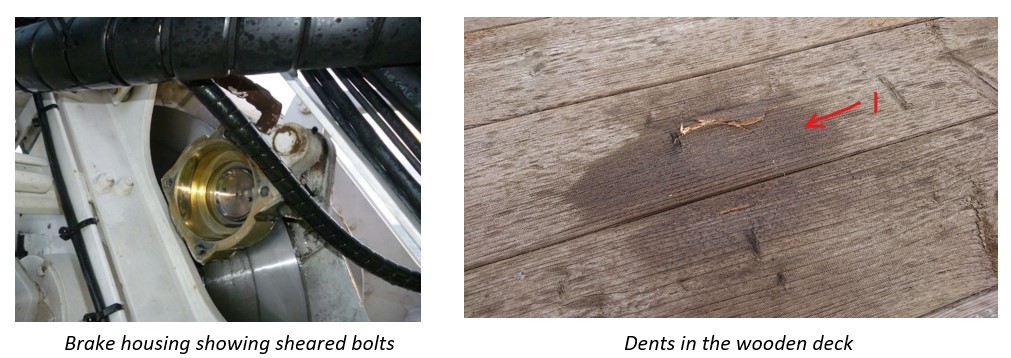
What went wrong?
Subsequent preliminary investigation by the manufacturer showed that the calliper had been subjected to significant hydraulic overpressure (up to 260 bar, as opposed to 170 bar design). Of the two pressure relief valves fitted to the man-riding brake system, which should have been adjusted during commissioning (the crane had been in service for only six months), one had a loose locking nut, the other was found screwed fully in, suggesting neither had been correctly set.
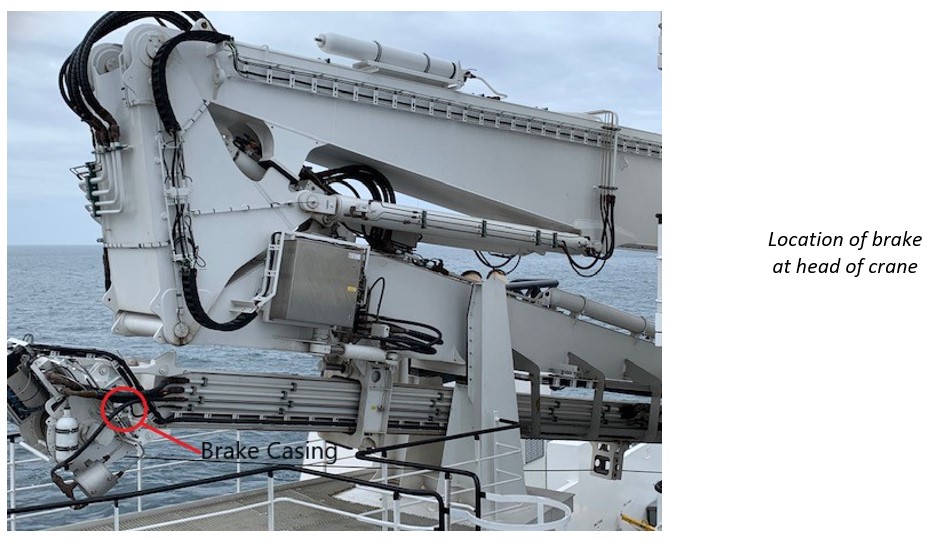
During the commissioning phase, adjustments are made to the AOPS (Automatic Overload Protection System) function of the crane. The Caliper disc brake is in the same part of the hydraulic circuit as the AOPS function and is therefore influenced by these adjustments.
The manufacturer’s technical investigation concluded that the likelihood of failure would have been greatly reduced, had adjustments been made on a hardware basis, rather than hydraulically.
It is likely that the bolts holding the calliper assembly together failed due to repeated overloading.
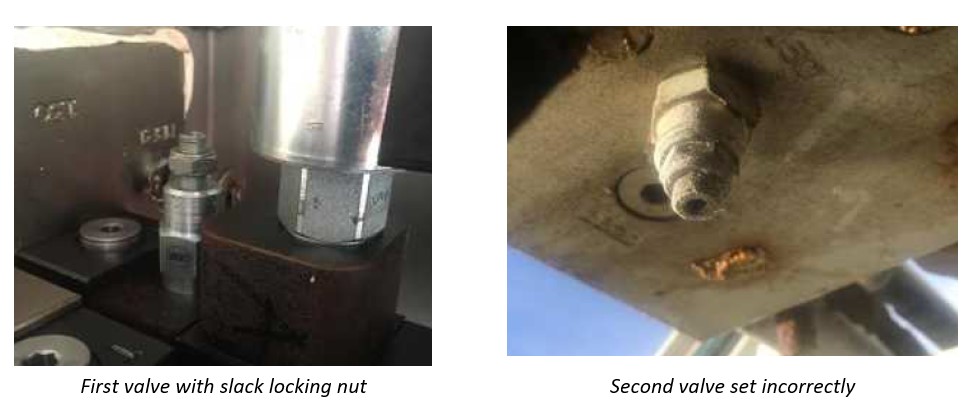
What were the causes of the incident?
- Immediate – hydraulic pressure relief valves failing to operate;
- Root – Changes made during commissioning were not evaluated thoroughly.
Actions and lessons learned
- Affected lines were isolated by blanking. allowing safe continued use for general loads, although no man-riding can take place;
- Ensure all pressure-relief valves are correctly adjusted, in order to prevent further overloading;
- Advise manufacturer reviews robustness of Management of change (MoC) and commissioning procedures; and personnel competence;
- Review on-board maintenance procedures for suitability;
- Advise manufacturer to verify correct adjustment of valves on other installations.
Safety Event
Published: 4 September 2020
Download: IMCA SF 26/20
IMCA Safety Flashes
Submit a Report
IMCA Safety Flashes summarise key safety matters and incidents, allowing lessons to be more easily learnt for the benefit of all. The effectiveness of the IMCA Safety Flash system depends on Members sharing information and so avoiding repeat incidents. Please consider adding [email protected] to your internal distribution list for safety alerts or manually submitting information on incidents you consider may be relevant. All information is anonymised or sanitised, as appropriate.
IMCA’s store terms and conditions (https://www.imca-int.com/legal-notices/terms/) apply to all downloads from IMCA’s website, including this document.
IMCA makes every effort to ensure the accuracy and reliability of the data contained in the documents it publishes, but IMCA shall not be liable for any guidance and/or recommendation and/or statement herein contained. The information contained in this document does not fulfil or replace any individual’s or Member's legal, regulatory or other duties or obligations in respect of their operations. Individuals and Members remain solely responsible for the safe, lawful and proper conduct of their operations.