High potential stored energy incident: inner buoyancy module clamp failure during removal
A member has reported an incident in which a clamp failed, allowing four objects to be ejected in various directions within the worksite. One of the objects struck a rigger on the back. The incident occurred during riser recovery using a Vertical Lay System (VLS). As part of the riser recovery process various ancillary items were removed from the riser prior to it being spooled through a tensioner system to a storage reel. Among the items to be removed were riser buoyancy modules which consist of two outer shells and an inner clamp.
During this recovery process, the incident occurred during removal of the final inner clamp. As a clamp securing strap was being cut, it failed unexpectedly causing the four inner parts of the clamp to fly off in various directions.
Fortunately there were no significant injuries; however there was clearly potential for two or more persons to have been seriously injured.
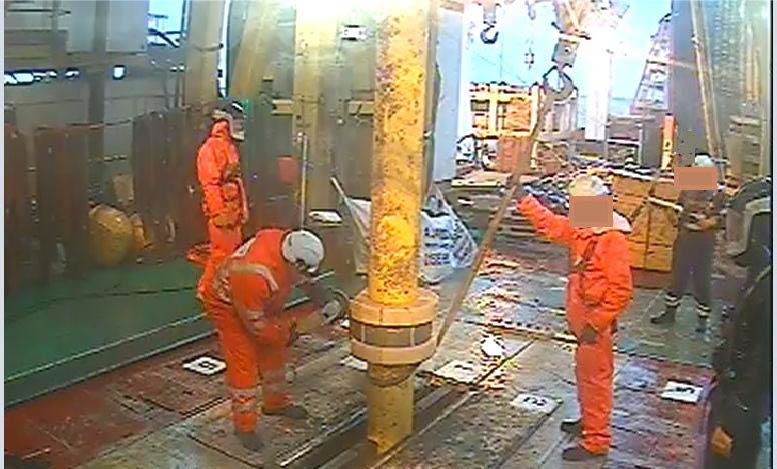
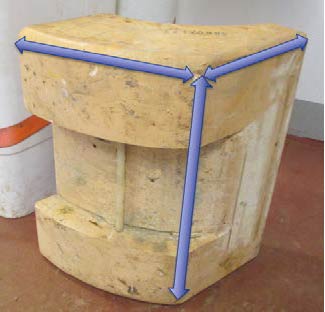
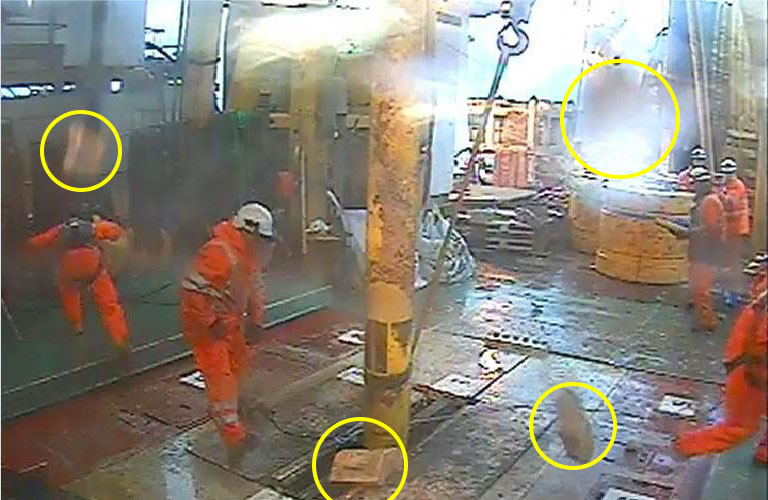
Our member’s on-going investigation has thus far revealed the following:
- Recent changes to the methodology for removing the clamp were not subject to a Management of Change process;
- These changes were not seen as significant enough to warrant the Management of Change process; however the changes introduced hazards which had not been risk assessed;
- The sling fitted below the clamp was over tensioned causing an upward force to be applied and ultimately the clamp to fail unexpectedly;
- The change to use the sling to stop the clamp falling to deck once cut was perceived as an improvement but the potential risks introduced by this change were not considered.
Our member noted that although this task (removing buoyancy modules) had been undertaken without incident hundreds of times during this year alone, the incident acted as a reminder of the need to guard against complacency, remain vigilant at all times and remain aware of our surroundings.
If there are any doubts about the operation take the time to stop work and reassess the situation. Any changes to procedures should be subject to the Management of Change process regardless of how minor they may initially appear.
Our member took the following actions:
- Reassessed the availability of task procedures and risk assessments;
- Checked on how well crews understood the above and how they reflect the way the job is actually being carried out;
- Ensured that when changes are made to improve how a task is carried, that all possible negative effects are fully considered;
- Ensured that during development of new procedures, adequate consideration is given to getting input from end users.
Members may wish to refer to the following similar incidents involving the sudden and unplanned release of stored energy (key words: released, stored, energy):
Safety Event
Published: 7 August 2014
Download: IMCA SF 14/14
IMCA Safety Flashes
Submit a Report
IMCA Safety Flashes summarise key safety matters and incidents, allowing lessons to be more easily learnt for the benefit of all. The effectiveness of the IMCA Safety Flash system depends on Members sharing information and so avoiding repeat incidents. Please consider adding [email protected] to your internal distribution list for safety alerts or manually submitting information on incidents you consider may be relevant. All information is anonymised or sanitised, as appropriate.
IMCA’s store terms and conditions (https://www.imca-int.com/legal-notices/terms/) apply to all downloads from IMCA’s website, including this document.
IMCA makes every effort to ensure the accuracy and reliability of the data contained in the documents it publishes, but IMCA shall not be liable for any guidance and/or recommendation and/or statement herein contained. The information contained in this document does not fulfil or replace any individual’s or Member's legal, regulatory or other duties or obligations in respect of their operations. Individuals and Members remain solely responsible for the safe, lawful and proper conduct of their operations.