Lost time injury (LTI) to leg
A member has reported an incident in which a sub-contractor’s employee suffered a leg injury which was categorised as a lost time injury (LTI). Whilst working on offloading a vessel, the sub-contract employee’s left leg above the ankle was pinned between a shifting spreader bar frame and a freight container located adjacent to the spreader bar frame. While one of the seven spreader bars was being lifted and in the air the remaining bars shifted, causing the frame to slide approximately one metre (40 inches) towards the freight container where the employee was standing. Hydraulic power packs were used to help free the trapped employee, who was taken to the local hospital. The employee suffered a hairline fracture of the left ankle and the incident was categorised as an LTI.
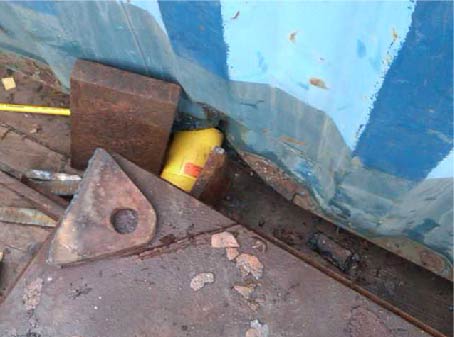
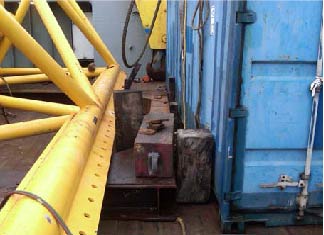
Following investigation, the company noted the following:
- The supervisor in charge did not follow in-house job safety analysis procedures;
- The sub-contractor personnel were not required to follow in-house job safety analysis procedures;
- The sub-contractor did not provide the specified fully trained personnel but, rather, a general labourer.
The company implemented the following actions to prevent recurrence:
- Installation of clips to secure the load frames to the deck and installed additional safety stops on the load frames to hold the spreader bars from moving
- Audit of training records of all sub-contractor personnel in order to ensure that personnel without proven competence or proper training were not accepted for work;
- The sub-contractor was asked to provide full training for all contract personnel, which should be:
- appropriate to the work being performed
- compliant with local regulatory safety standards
- fully verifiable through testing;
- Senior leadership would provide clear guidance to supervisory personnel that safety processes and procedures could not be cut short.
Safety Event
Published: 22 December 2009
Download: IMCA SF 18/09
IMCA Safety Flashes
Submit a Report
IMCA Safety Flashes summarise key safety matters and incidents, allowing lessons to be more easily learnt for the benefit of all. The effectiveness of the IMCA Safety Flash system depends on Members sharing information and so avoiding repeat incidents. Please consider adding [email protected] to your internal distribution list for safety alerts or manually submitting information on incidents you consider may be relevant. All information is anonymised or sanitised, as appropriate.
IMCA’s store terms and conditions (https://www.imca-int.com/legal-notices/terms/) apply to all downloads from IMCA’s website, including this document.
IMCA makes every effort to ensure the accuracy and reliability of the data contained in the documents it publishes, but IMCA shall not be liable for any guidance and/or recommendation and/or statement herein contained. The information contained in this document does not fulfil or replace any individual’s or Member's legal, regulatory or other duties or obligations in respect of their operations. Individuals and Members remain solely responsible for the safe, lawful and proper conduct of their operations.