Lost time injury (LTI): Winch base plate failure
A member has reported an incident in which a winch base plate failed catastrophically, causing serious injuries to a nearby crewman. The incident occurred when the vessel was stern to shore, unreeling pipe from an onboard reel onto the shore. During this process, a winch was used to disconnect the end of the pipe from the reel, and tail the head from the reel while the Vertical Lay System (VLS) tension machine paid out the pipe. When the end of the pipe reached the top of the VLS aligner a ‘controlled stop’ was called for by the winch operator. The winch operator relayed to his supervisor that he felt the winch base plate flexing. After the winch came to ‘all stop’ the welds on the winch base plate securing it to the deck failed; the winch was forcefully pulled forward and up and came to rest forward of the reel well. The winch operator had his right foot on the base plate and was thrown up by the force suffering a serious injury to his left knee and lower leg.
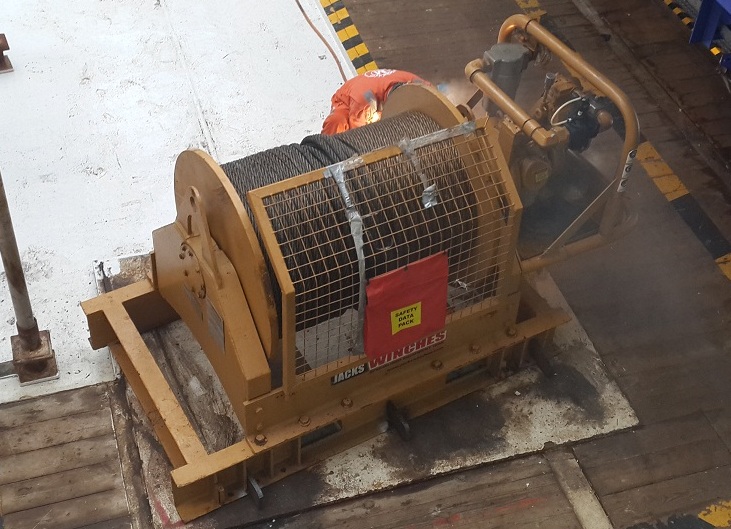
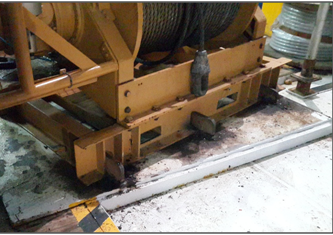
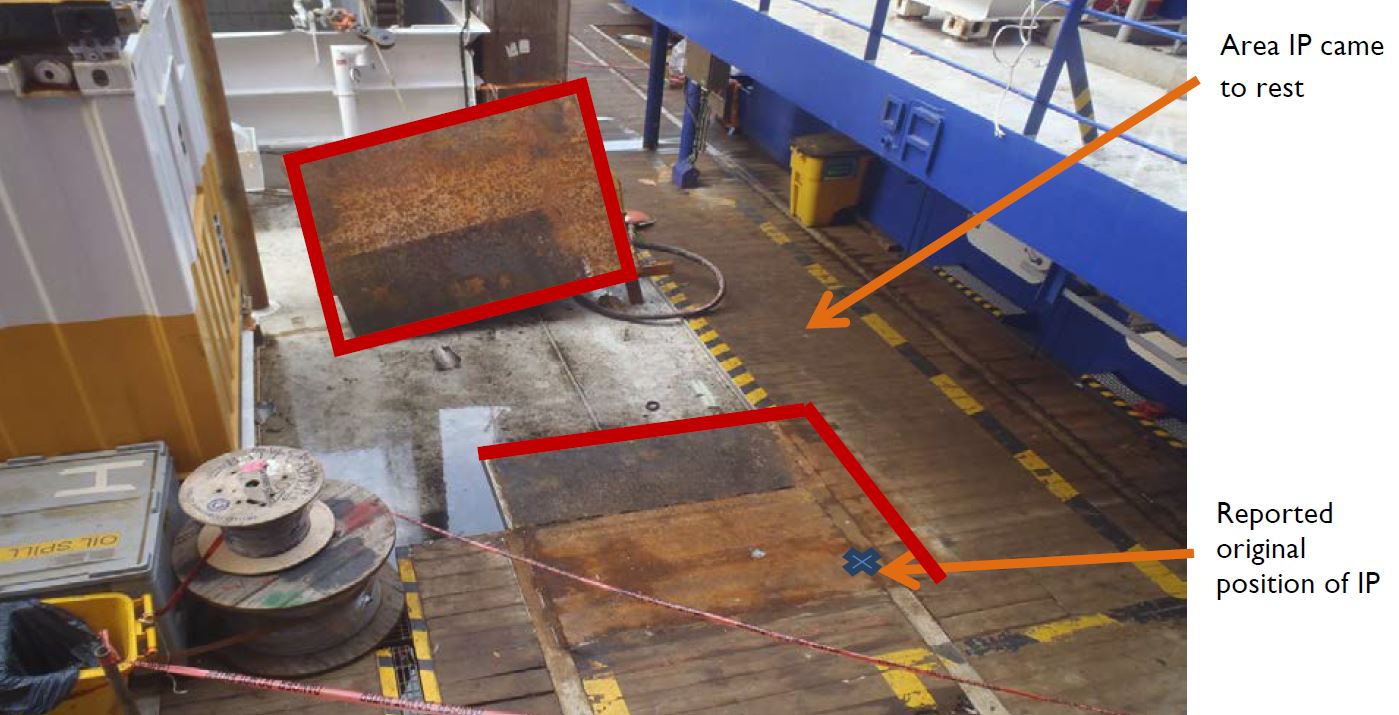
Our member’s investigation revealed the following:
- A repeatedly malfunctioning 32t constant-tension lay system winch had been replaced with a 10t air tugger non-constant tension winch for use in offloading pipeline. The 10t winch had been initially installed for loading purposes, and then maintained for offloading, as the 32t winch had not been repaired;
- Approximately two months before the incident the winch base plate and winch attachments deflected under load. Additional fastenings were welded from the winch frame to the base plate;
- Eight days prior to the incident the rental 10t winch had been installed, and MPI (magnetic particle inspection) checks [of the welding] were done between winch and base plate fastenings.
Our member noted the following causal factors:
- A 32t constant-tension winch repeatedly malfunctioned, was removed from service, and had been replaced with a 10t tugger winch;
- Management of Change (MOC) procedure raised but did not include design calculations for welded installation of base plate, attached between main deck and 10t winch;
- Replacement winch was not constant tension nor fitted with a tension measurement device;
- Cause of base plate deflection occurring two months prior to incident was not investigated and corrected;
- Inability of aligner load cells to accurately check tension at smaller tower angle (less than 80°);
- Calibration validation process had not been completed due to a load cell failure incident.
Our member’s recommendations and corrective actions were:
- Identify and correct shortcomings in MOC requirements;
- Ensure that non-destructive testing be carried out on all welds between winch base plates and decks whenever a winch is installed onto a base plate;
- Review and revise Pipe Loading and Offloading procedures to eliminate identified causal factors;
- Ensure vessel management and crew are fully apprised of ‘Stop the job’ or ‘Stop Work Authority’ policies and procedures;
- Re-design the lay system so that aligner load cells can be calibrated to allow tension checks for lower tower angles;
- Revise applicable procedures to include ‘Hold Points’ when load cells must be calibrated before undertaking any installation work involving the tower, including any work that requires the tower to go below 80 degrees.
Members may wish to refer to the following incidents (key words: weld, winch, base-plate, failure):
Safety Event
Published: 14 July 2014
Download: IMCA SF 12/14
IMCA Safety Flashes
Submit a Report
IMCA Safety Flashes summarise key safety matters and incidents, allowing lessons to be more easily learnt for the benefit of all. The effectiveness of the IMCA Safety Flash system depends on Members sharing information and so avoiding repeat incidents. Please consider adding [email protected] to your internal distribution list for safety alerts or manually submitting information on incidents you consider may be relevant. All information is anonymised or sanitised, as appropriate.
IMCA’s store terms and conditions (https://www.imca-int.com/legal-notices/terms/) apply to all downloads from IMCA’s website, including this document.
IMCA makes every effort to ensure the accuracy and reliability of the data contained in the documents it publishes, but IMCA shall not be liable for any guidance and/or recommendation and/or statement herein contained. The information contained in this document does not fulfil or replace any individual’s or Member's legal, regulatory or other duties or obligations in respect of their operations. Individuals and Members remain solely responsible for the safe, lawful and proper conduct of their operations.