Near-miss: Missing nut and split pin on shackle
A member has reported an incident in which rented lifting equipment was returned to the vendor (a winch supplier) with important parts missing. Rental equipment was returned to the winch supplier from a recent project, and the hydraulic winch set was delivered from the vessel with the split pin and nut missing from one of the 3.25Te shackles which were part of the winch lifting set.
When the equipment arrived at the supplier’s base on the back of a truck, the winch supplier offloaded the equipment safely via a forklift truck using the forklift pockets. They then carried out a visual inspection of the equipment and discovered the missing split pin and nut. No incident occurred, however, it is not known whether the lifting set was used in this degraded condition during vessel demobilisation, i.e. without the shackle being properly installed. This could have resulted in a dropped load incident. Additionally, there was the potential for a dropped object incident at the supplier’s base during offloading from the truck had the shackle bolt worked loose.
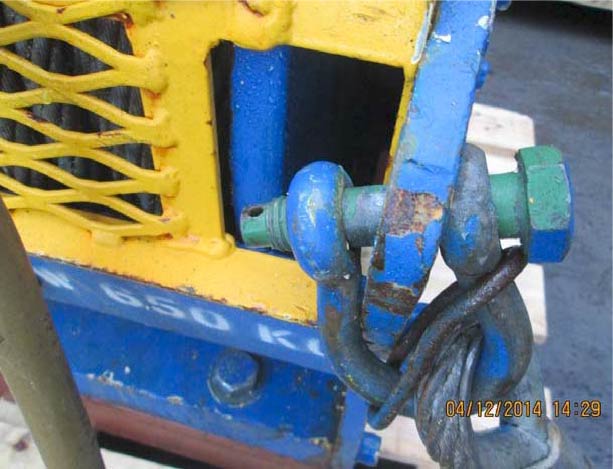
Our member’s investigation noted the following:
- There was no evidence that the rigging arrangement was incorrect during the demobilisation of the equipment from the vessel. However, this could not be ruled out and therefore it was vital that the importance of carrying out rigging checks prior to lifting is reiterated;
- It was possible that the split pin and nut worked themselves loose as a result of vibration on the back of the truck during road transportation. This would indicate that either the split pin was incorrectly fitted, or was missing.
Our member took the following actions:
- Subjected all rigging arrangements to a thorough visual inspection prior to carrying out any lifting, ensuring that split pins are securely in place to prevent nuts and bolts from working themselves loose;
- Ensured that lift supervisor inspects all loads thoroughly for potential dropped objects and to ensure correct rigging and slinging arrangements are in place and correctly secured;
- Reiterated importance of thorough visual checking of lifting equipment before use, before mobilisation and demobilisation.
Members should be aware of IMCA guidance and IMCA safety promotional material on lifting equipment, as follows:
- Guidelines for lifting operations
- Lifting operations (pocket card)
- Lifting equipment (pocket card)
Members may wish to refer to the following similar incidents (key words: missing, lifting):
Safety Event
Published: 5 February 2015
Download: IMCA SF 02/15
IMCA Safety Flashes
Submit a Report
IMCA Safety Flashes summarise key safety matters and incidents, allowing lessons to be more easily learnt for the benefit of all. The effectiveness of the IMCA Safety Flash system depends on Members sharing information and so avoiding repeat incidents. Please consider adding [email protected] to your internal distribution list for safety alerts or manually submitting information on incidents you consider may be relevant. All information is anonymised or sanitised, as appropriate.
IMCA’s store terms and conditions (https://www.imca-int.com/legal-notices/terms/) apply to all downloads from IMCA’s website, including this document.
IMCA makes every effort to ensure the accuracy and reliability of the data contained in the documents it publishes, but IMCA shall not be liable for any guidance and/or recommendation and/or statement herein contained. The information contained in this document does not fulfil or replace any individual’s or Member's legal, regulatory or other duties or obligations in respect of their operations. Individuals and Members remain solely responsible for the safe, lawful and proper conduct of their operations.