Snagging hazards
A member reports two unrelated incidents in which a causal factor was something getting caught or snagged in an unplanned way.
Incident 1: Corner of a container got snagged
On a vessel engaged in deck cargo operations offshore, a number of lifts had been successfully discharged and backloaded, which led to limited space on deck. The crane operator had landed a 3m cargo container on deck, and while he was trying to re-position the lift for easy disconnection by the deck crew, the corner of the container became snagged on the side of a deck light guard resulting in the parting of one of the slings. The container with broken slings was safely stowed on deck. There were no injuries, no damage and no environmental impact.
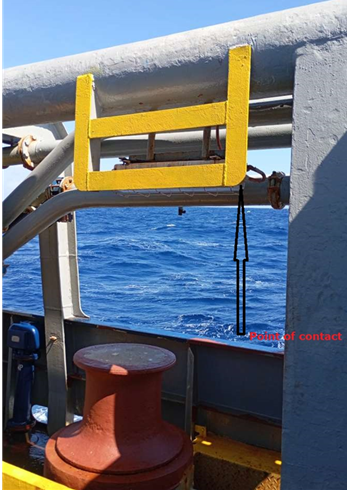
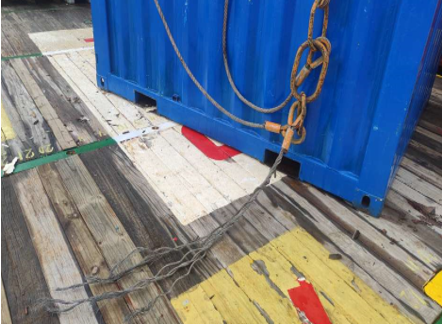
What went wrong
- The crane operator did not notice the potential snagging point, so continued the operation;
- The deck crew did not recognize hazard and did not stop the activity;
- Owing to the colour it was painted, the deck light guard may have been difficult for the crane operator to see and identify as a potential snagging point.
Lessons
The importance of the crane operator being able to see the job, and to have good communications with the deck crew, cannot be overstated.
Members may wish to refer to:
Incident 2: Anchor chain parted after snagging on PPE
The starboard anchor chain of a tug boat snapped, causing loss of the anchor. CCTV footage reveals that during mooring operations, the crotch strap of a worker’s lifejacket got caught on the lever of the anchor clutch, slightly engaging it. This put tension on the anchor chain during the operation of the winch, which subsequently caused it to part. There were no injuries and no other property damage.
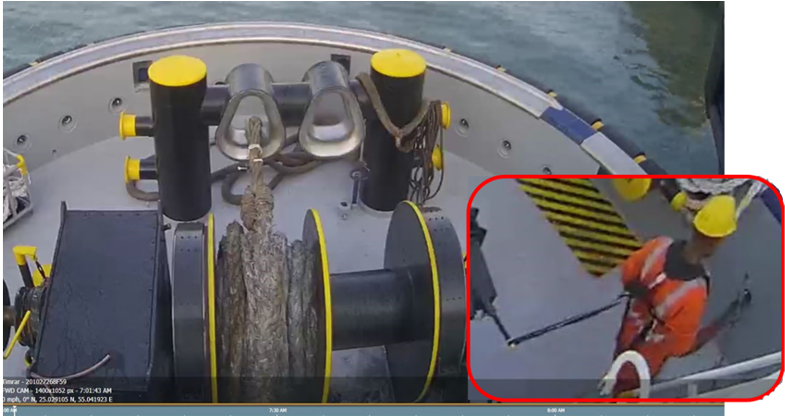
What went wrong
- There was no “securing pin” that would have prevented the clutch from engaging;
- A pre-use check inspection had not been carried out.
Actions
- Inspect all vessels’ anchor winches to confirm the availability of securing pins;
- Ensure pre-inspection takes place on all similar winches to ensure they are disengaged prior to operation;
- Ensure that the securing pin size is adequate and not undersized, to prevent the clutch from engaging unintentionally.
Members may wish to refer to:
Safety Event
Published: 11 November 2024
Download: IMCA SF 22/24
IMCA Safety Flashes
Submit a Report
IMCA Safety Flashes summarise key safety matters and incidents, allowing lessons to be more easily learnt for the benefit of all. The effectiveness of the IMCA Safety Flash system depends on Members sharing information and so avoiding repeat incidents. Please consider adding [email protected] to your internal distribution list for safety alerts or manually submitting information on incidents you consider may be relevant. All information is anonymised or sanitised, as appropriate.
IMCA’s store terms and conditions (https://www.imca-int.com/legal-notices/terms/) apply to all downloads from IMCA’s website, including this document.
IMCA makes every effort to ensure the accuracy and reliability of the data contained in the documents it publishes, but IMCA shall not be liable for any guidance and/or recommendation and/or statement herein contained. The information contained in this document does not fulfil or replace any individual’s or Member's legal, regulatory or other duties or obligations in respect of their operations. Individuals and Members remain solely responsible for the safe, lawful and proper conduct of their operations.