Unsafe lifting operations
A member reports two incidences of unsafe lifting, which are worthy of note.
Incident 1 Unsafe Lifting Operations By sub-contractor
On a platform supply vessel (PSV) involved in demobilization operations alongside, the crane operator attempted to lift a winch frame located on at the main deck while there was scaffolding structure still over the winch frame. In addition, crew were still dismantling the scaffolding and so were in the line of fire. Upon observing this unsafe condition the job was immediately stopped by the vessel team.
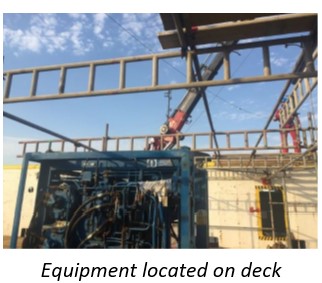
What were the causes? What went wrong?
- Line of fire – there was scaffolding over the lifting area and the presence of personnel in the line of fire was not considered by the contractor;
- Incorrect lifting method – scaffolding pipes were placed under the winch platform with the purpose to roll it over with partial lifting, creating a risk of the winch sliding back off its platform as it was not welded on it;
- People were in a rush – the contractor’s lifting crew were in a hurry to complete the job on that day, as windy weather was forecast for the next day.
Actions taken and lessons learned:
- SIMOPS! Take into account what else is happening around you. Avoid any conflicting activities during any lifting operations;
- All lifting operations should be properly planned and risk assessed.
Incident 2 Master Stopped Unsafe Lifting Operation
A client’s lifting crew attempted to load a metal structure to the vessel deck. The operation was stopped by the vessel Master. He questioned the certification of the lifting point and the lifting gear, as having no colour code signs. As no certificates could be provided, the vessel Master refused cargo and took the matter up with company management and the client’s representatives.
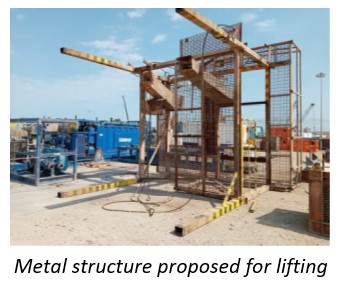
Actions taken and lessons learned:
- Crew to conduct vessel inspections to ensure valid colour code applied to all lifting equipment and accessories, as per Safety management system;
- Reiterate the importance of checking lifting equipment condition before and after the task.
Related Resources
Members may wish to refer to
- “Are you prepared to work safely?” videos: Lifting equipment Lifting operations
- IMCA SEL 019 Guidelines for lifting operations
- Lifting bridle snagged – failure to “stop the job”
- Near miss: unexpected lowering of a suspended load
Safety Event
Published: 28 September 2020
Download: IMCA SF 28/20
IMCA Safety Flashes
Submit a Report
IMCA Safety Flashes summarise key safety matters and incidents, allowing lessons to be more easily learnt for the benefit of all. The effectiveness of the IMCA Safety Flash system depends on Members sharing information and so avoiding repeat incidents. Please consider adding [email protected] to your internal distribution list for safety alerts or manually submitting information on incidents you consider may be relevant. All information is anonymised or sanitised, as appropriate.
IMCA’s store terms and conditions (https://www.imca-int.com/legal-notices/terms/) apply to all downloads from IMCA’s website, including this document.
IMCA makes every effort to ensure the accuracy and reliability of the data contained in the documents it publishes, but IMCA shall not be liable for any guidance and/or recommendation and/or statement herein contained. The information contained in this document does not fulfil or replace any individual’s or Member's legal, regulatory or other duties or obligations in respect of their operations. Individuals and Members remain solely responsible for the safe, lawful and proper conduct of their operations.