Sheave became detached during lifting operations
What happened
During recovery operations of marine geophysical sensors, a sheave parted from a swivel connection on the A-frame. The sheave fell approximately 6m to the deck below. No personnel were underneath the sheave, however had the sheave struck an individual, it could have caused serious injury.
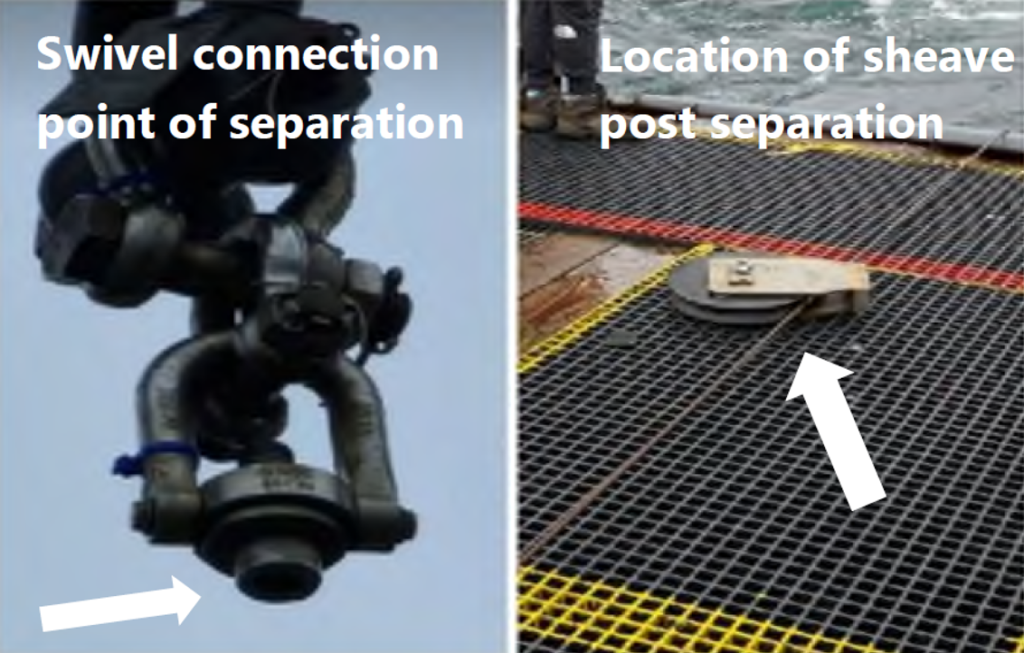
What went wrong
- Investigation revealed that:
- Installation of the sheave and introduction of new components had not been subject to a documented management of change;
- There were no written installation instructions provided with the sheave, with nothing detailing the configuration of the sheave to the swivel connection;
- The person installing the sheave relied on verbal instructions and an incorrect understanding of the previous installation;
- When the sheave was installed, the secondary retention (securing sling) was considered unnecessary and removed – there was no independent verification / quality check (QC) carried out;
- Prior to the incident, there had been numerous opportunities including one by an independent (third party) inspector to identify that the sheeve was incorrectly installed;
- There was inadequate development and control of the lifting equipment records / register.
Actions taken/recommendations
- Equipment – Design changes were made after the incident to remove the swivel connection and replace it with a pad eye thereby reducing the potential for incorrect connection;
- Secondary securing slings were fitted to all sheaves. Additionally, a cable was installed between the A-frame legs to act as another barrier should primary and secondary retention fail. The sensor tow wire straddles this cable, so if the sheave falls it slides down the tow cable rather than drop (see image below).
- Monitoring, tracking, inspecting, and provision of guidance for lifting equipment, accessories and rigging was improved.
- Procedures – Written installation and maintenance instructions should be provided with all equipment/sheaves.
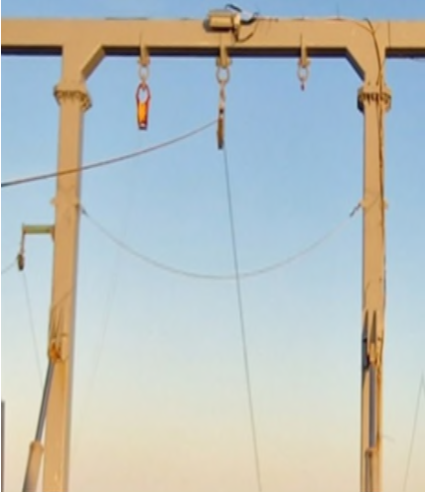
Our member held a safety stand down wherein there was discussion relating to the need for and importance of:
- properly managing lifting equipment, accessories, and associated records / registers;
- carrying out post-installation quality assurance checks;
- installation of secondary securing – designed to restrain the item should the primary fixing fail;
- personnel remaining out of the line of fire;
- following established procedures and work instructions – where none exist, or if there is any doubt, speak up and request the required information.
Members may wish to refer to
Safety Event
Published: 21 June 2023
Download: IMCA SF 15/23
IMCA Safety Flashes
Submit a Report
IMCA Safety Flashes summarise key safety matters and incidents, allowing lessons to be more easily learnt for the benefit of all. The effectiveness of the IMCA Safety Flash system depends on Members sharing information and so avoiding repeat incidents. Please consider adding [email protected] to your internal distribution list for safety alerts or manually submitting information on incidents you consider may be relevant. All information is anonymised or sanitised, as appropriate.
IMCA’s store terms and conditions (https://www.imca-int.com/legal-notices/terms/) apply to all downloads from IMCA’s website, including this document.
IMCA makes every effort to ensure the accuracy and reliability of the data contained in the documents it publishes, but IMCA shall not be liable for any guidance and/or recommendation and/or statement herein contained. The information contained in this document does not fulfil or replace any individual’s or Member's legal, regulatory or other duties or obligations in respect of their operations. Individuals and Members remain solely responsible for the safe, lawful and proper conduct of their operations.