Unexpected Descent and Ascent of Mattress Lifting Frame
What happened?
A subsea load close to working divers started moving with no intervention from the crane operator. The incident occurred during movement of concrete mattresses using a mattress handling frame and the Main Crane. The frame was held with the vessel crane set-up in Active Heave Compensation (AHC) mode, at approximately 3m above seabed. Divers were in the process of reconnecting the hooks to the mattress handling frame ahead of recovery to deck when the frame was seen to descend to 1m depth above seabed. An “all stop”, followed by a “come up on the crane” command was issued and within 3 seconds of the command the frame was observed to ascend at an unexpected rate back to its original position approx. 3m above seabed without crane operator input on the joystick. Both Diver 1 and Diver 2 were in close proximity to the frame just before it ascended. There were no injuries nor damage to equipment or subsea assets.
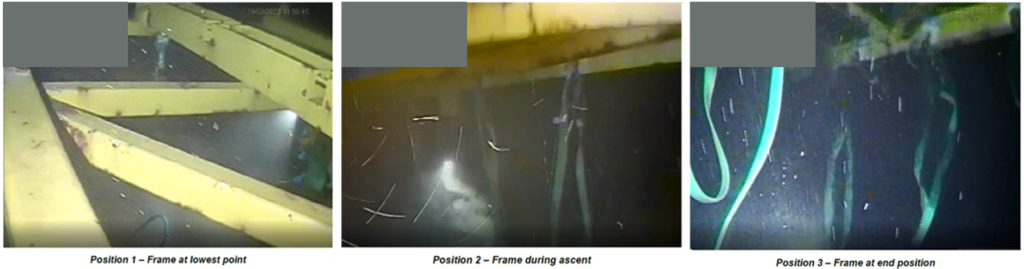
What went wrong
- The crane software design was such that pressing the controller lock when in AHC mode, had an unintended impact on winch motor displacement control. Engaging controller lock caused the load to slowly creep/pay out without joystick input. Disengaging controller lock caused the load to abruptly pay in and return to its original position;
- This software interaction was not amended through update/patching of the software when it was first identified, as it was considered to be controlled sufficiently through a Crane Operating Manual update only;
- There was a failure of the document control process for the Crane Operating Manual, such that obsolete revisions were in circulation and available for use – an incorrect revision of the manual was issued to the new Crane Operator. This revision advised that Controller Lock can be used when in AHC and that the load will remain stationary (subsequent revisions of the Manual highlight that it should not be used in AHC due to it causing abrupt movement);
- The familiarisation process did not trigger a discussion about known operating sensitivities, defects, or differences in the on-board crane systems from those the new operator may be familiar with.
What were the causes?
Our member drew the following conclusions regarding causes:
- Immediate cause – use of the controller lock function whilst operating in AHC mode;
- Underlying causes:
- Unintended consequences of crane software design which had not been “patched” or updated;
- Incorrect version of the Operating Manual issued to the Crane Operator;
- Familiarisation did not inform Crane Operator not to use the controller lock function.
- Root causes:
- Technical: System / software interaction issue;
- Organisational: Deficiency in document control – resulted in obsolete revisions being in circulation and given to Crane Operator;
- People: Decision making – matter was previously identified but considered to be controlled sufficiently by Crane Manual update only.
Lessons and actions
- Proper control of Operating Manual revisions to ensure that the latest revisions are in circulation and available for use, with obsolete revisions removed from service;
- Review and update familiarisation/handover process to include additional items to trigger discussion between new Operators and verifiers about operating sensitivities, known anomalies or system differences;
- Where there is a known mechanical and or procedural gap, ensure it is highlighted and addressed immediately to eliminate the issue. Ensure all on-signing Crane Operators are briefed on the incident, the causal factors and corrective/preventive measures;
- Installation of button flip-cover over Controller Lock function and additional signage to be placed within the Crane Cabin.
Members may wish to refer to
Safety Event
Published: 3 August 2023
Download: IMCA SF 19/23
IMCA Safety Flashes
Submit a Report
IMCA Safety Flashes summarise key safety matters and incidents, allowing lessons to be more easily learnt for the benefit of all. The effectiveness of the IMCA Safety Flash system depends on Members sharing information and so avoiding repeat incidents. Please consider adding [email protected] to your internal distribution list for safety alerts or manually submitting information on incidents you consider may be relevant. All information is anonymised or sanitised, as appropriate.
IMCA’s store terms and conditions (https://www.imca-int.com/legal-notices/terms/) apply to all downloads from IMCA’s website, including this document.
IMCA makes every effort to ensure the accuracy and reliability of the data contained in the documents it publishes, but IMCA shall not be liable for any guidance and/or recommendation and/or statement herein contained. The information contained in this document does not fulfil or replace any individual’s or Member's legal, regulatory or other duties or obligations in respect of their operations. Individuals and Members remain solely responsible for the safe, lawful and proper conduct of their operations.